lookforjoe
True Classic
Today I added some fibre-reinforced bondo in the larger voids - around the surround & under the marker light
couple layers of regular bondo/sand later. Center rib needs more filler to level across the span
Still have to add more, and fix the wonky directional aperture
Left looks pretty good overall
little primer on the right to check flow into center & top. Gonna need much clean up & detail later. Left side needs more work
Feeling OK about the way it's coming along!
Spoiler & uprights will go in like this. Have to add some sort of attachment method for the uprights under the fixed sections.
also have to figure out how to resolve this, since it has no continuation in the fixed section
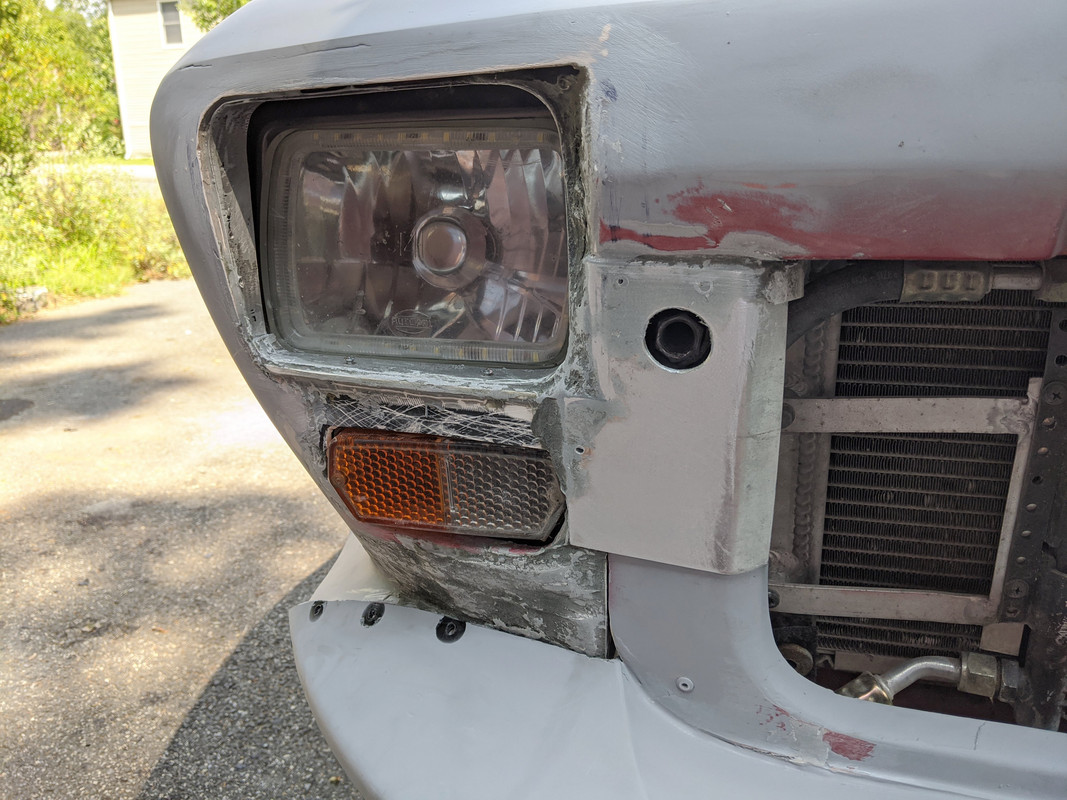
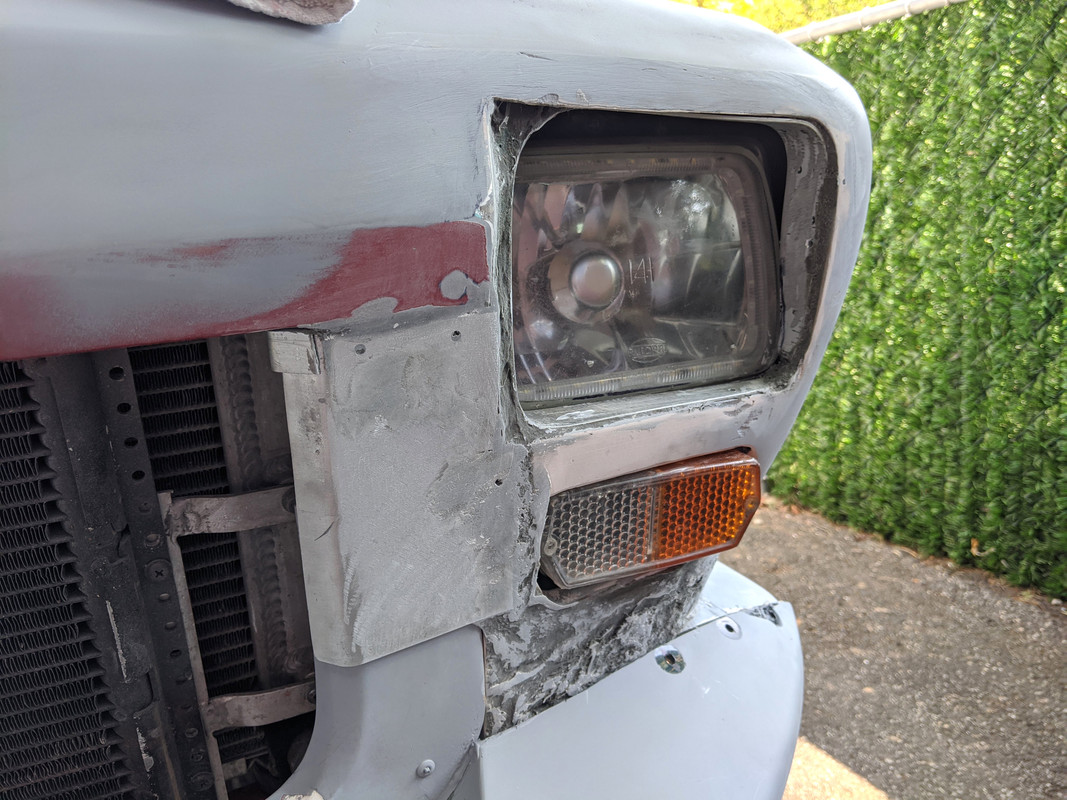
couple layers of regular bondo/sand later. Center rib needs more filler to level across the span
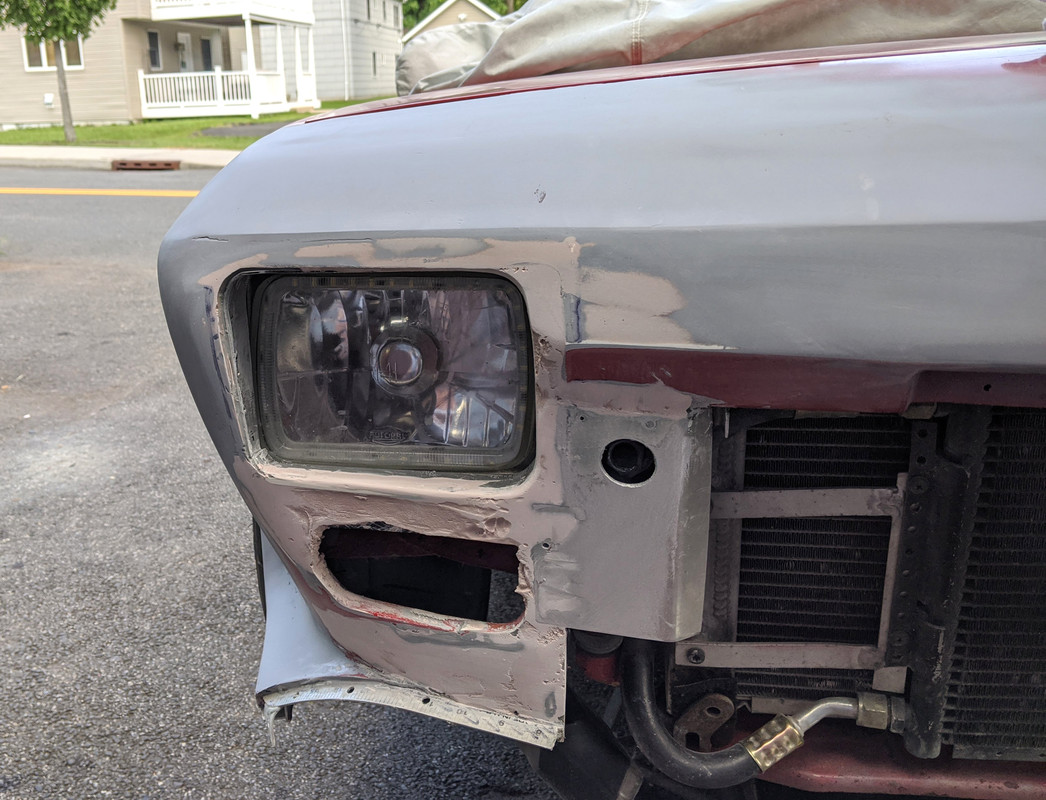
Still have to add more, and fix the wonky directional aperture
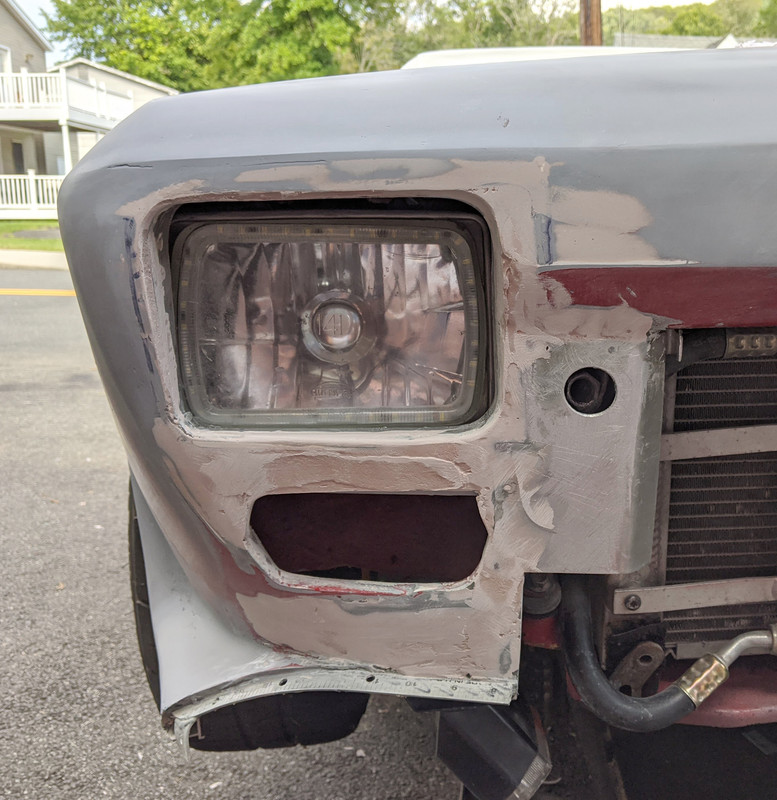
Left looks pretty good overall
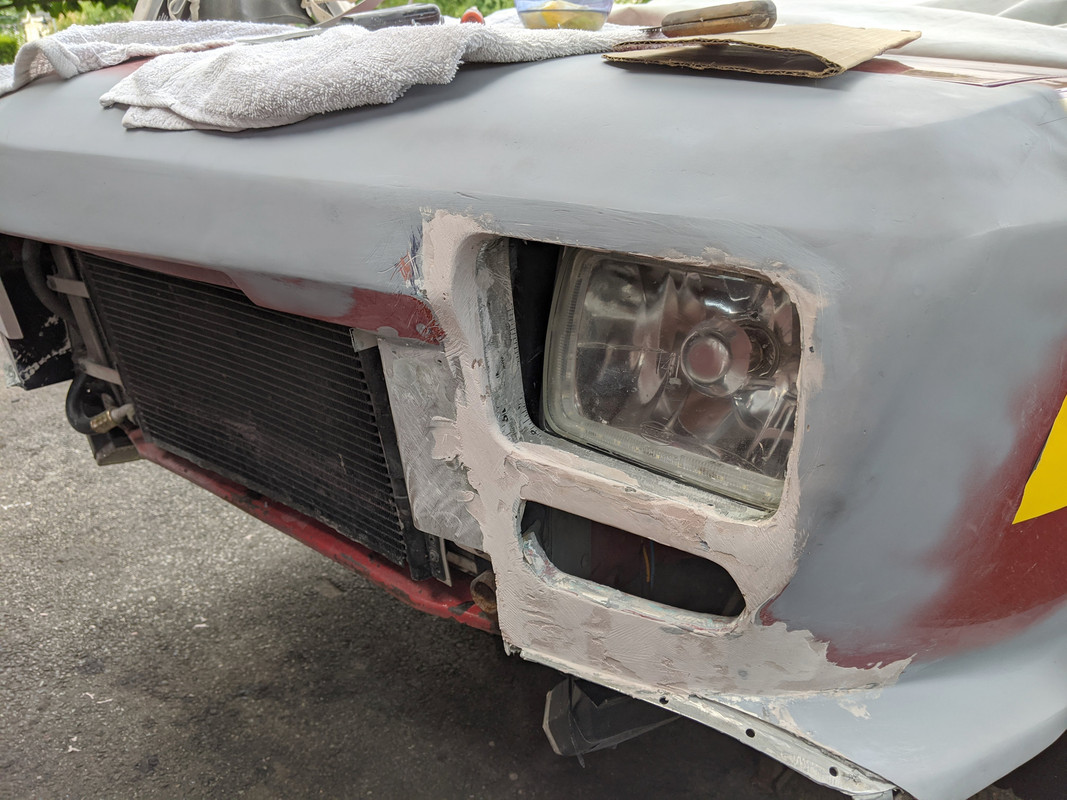
little primer on the right to check flow into center & top. Gonna need much clean up & detail later. Left side needs more work
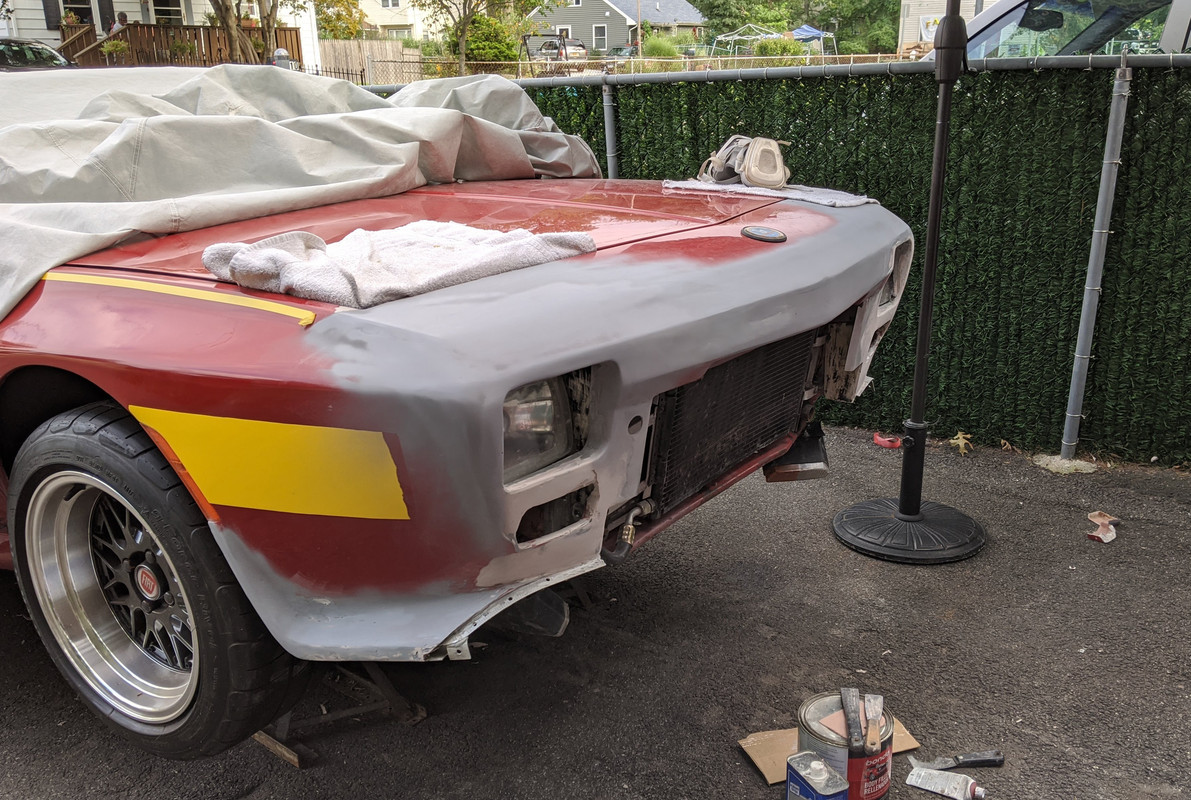
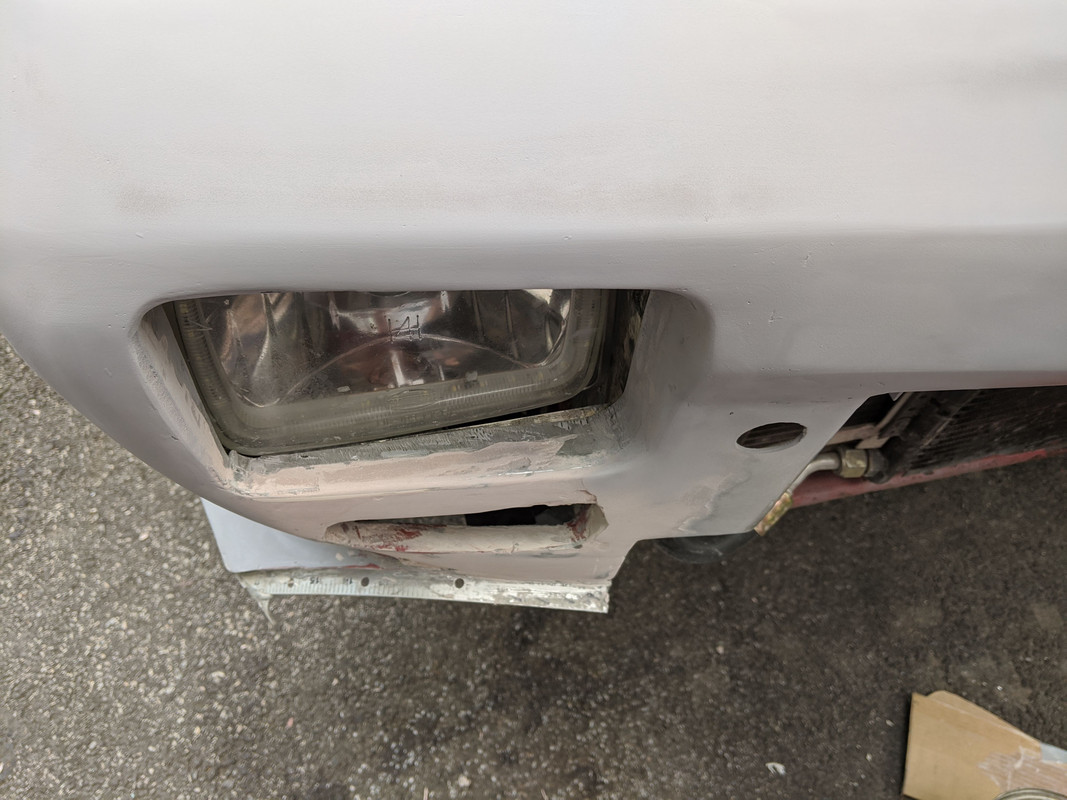
Feeling OK about the way it's coming along!
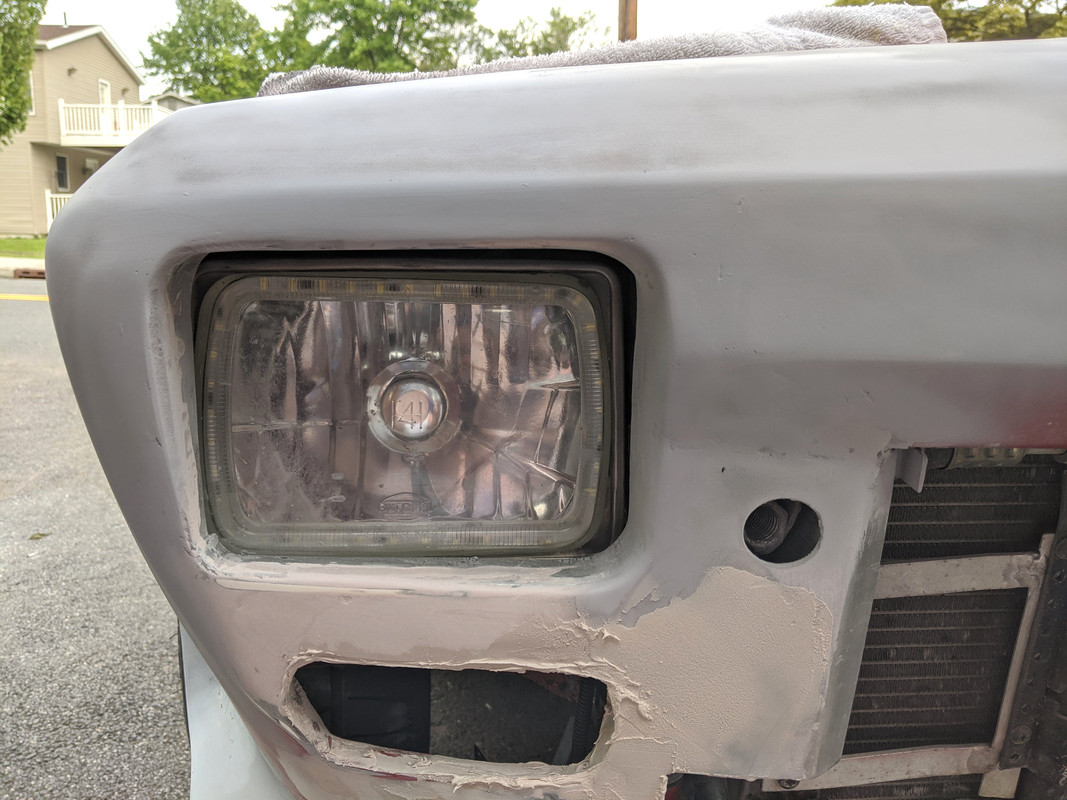
Spoiler & uprights will go in like this. Have to add some sort of attachment method for the uprights under the fixed sections.
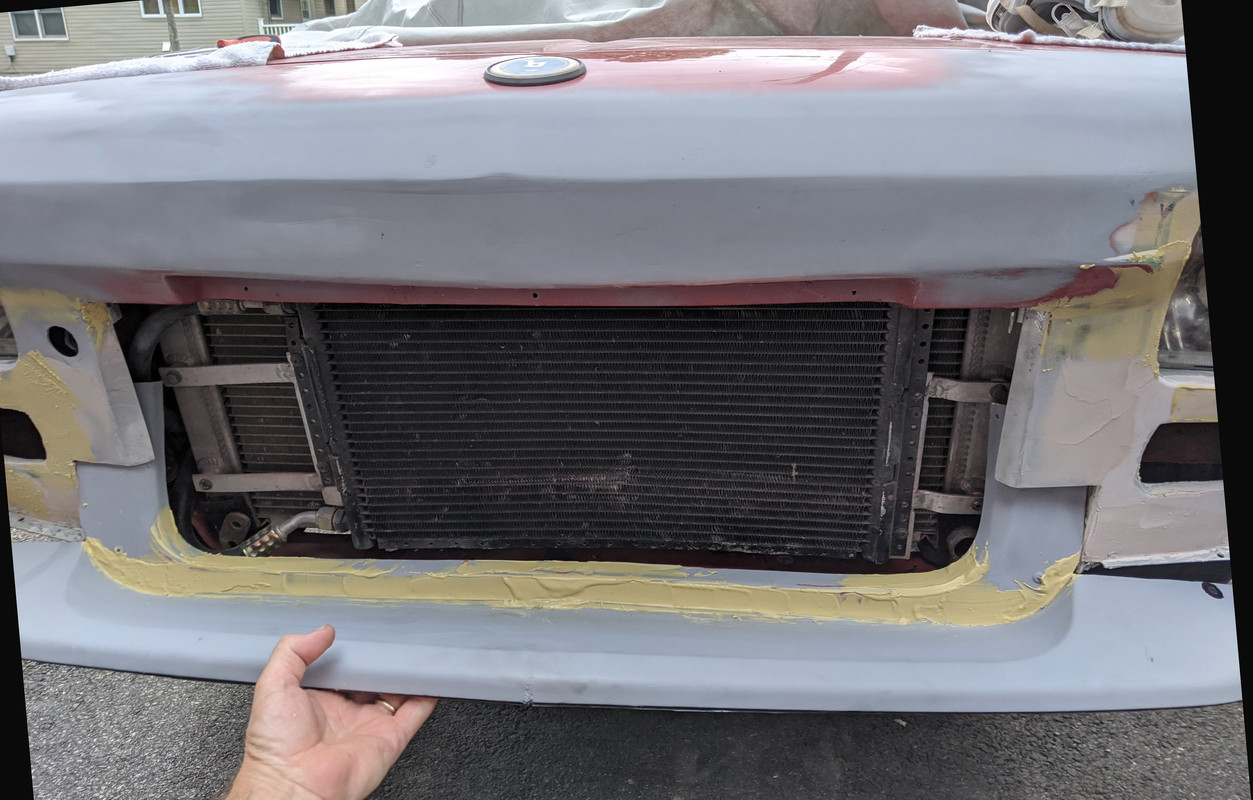
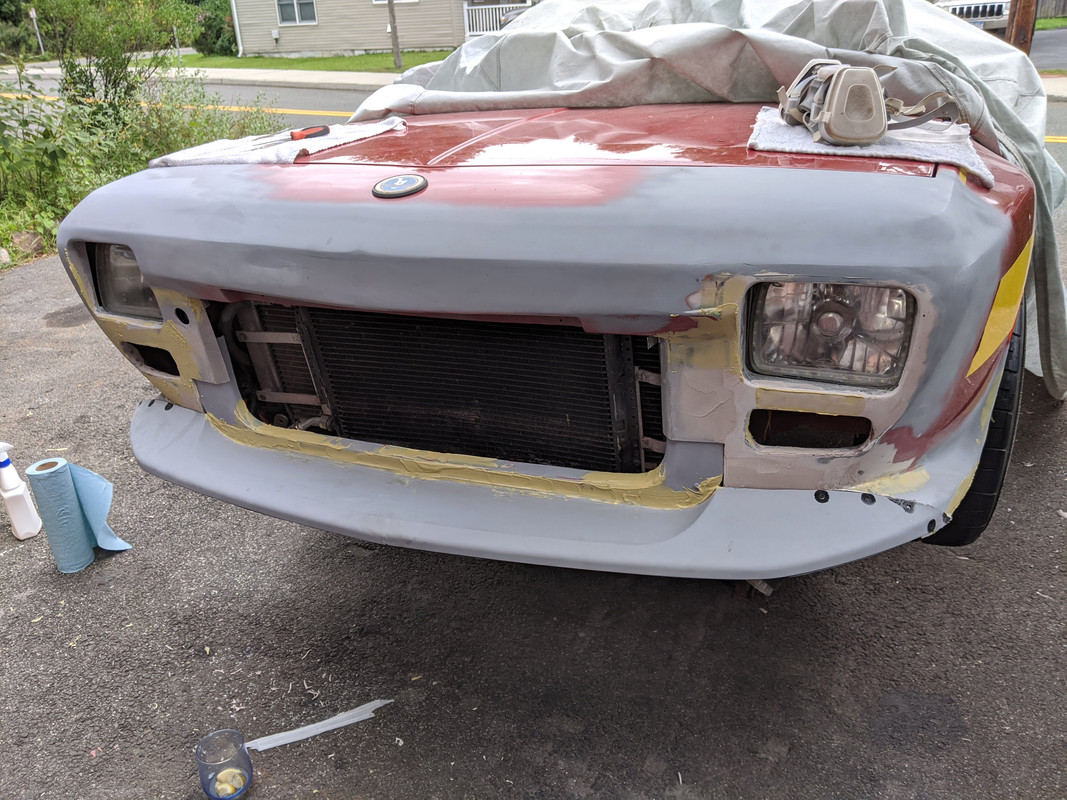
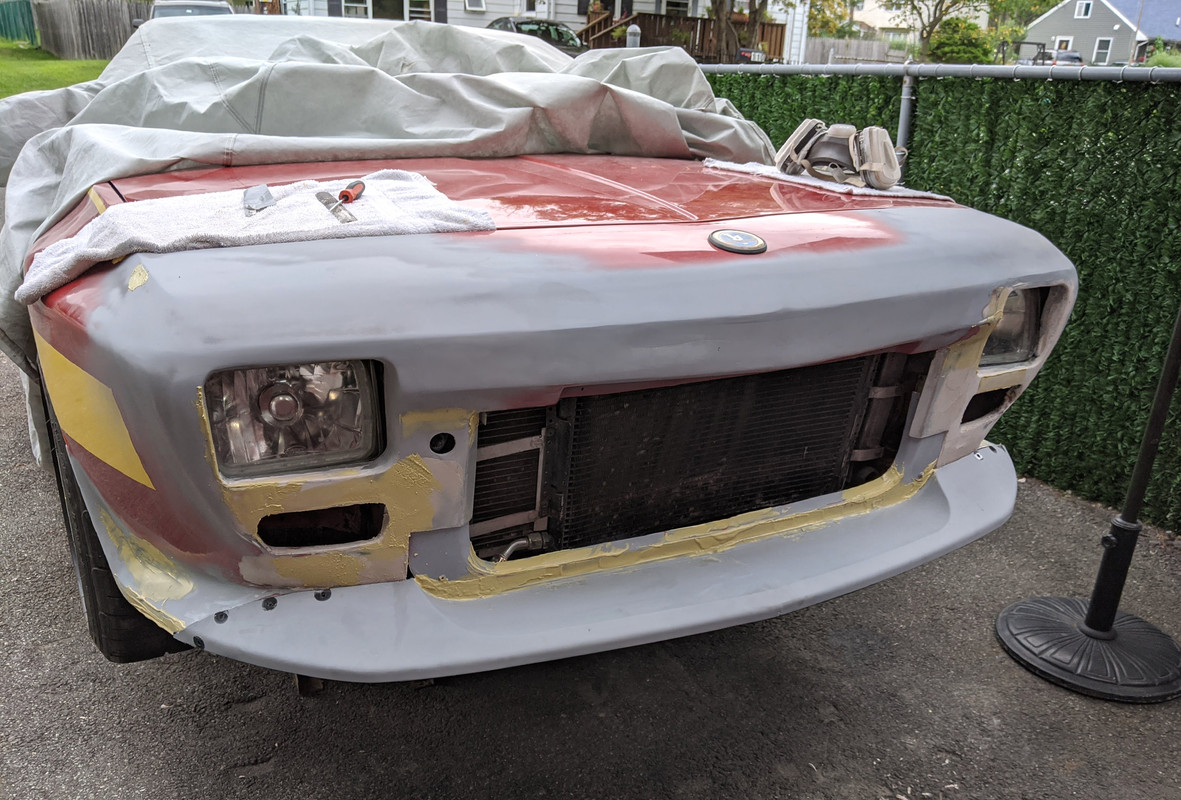
also have to figure out how to resolve this, since it has no continuation in the fixed section
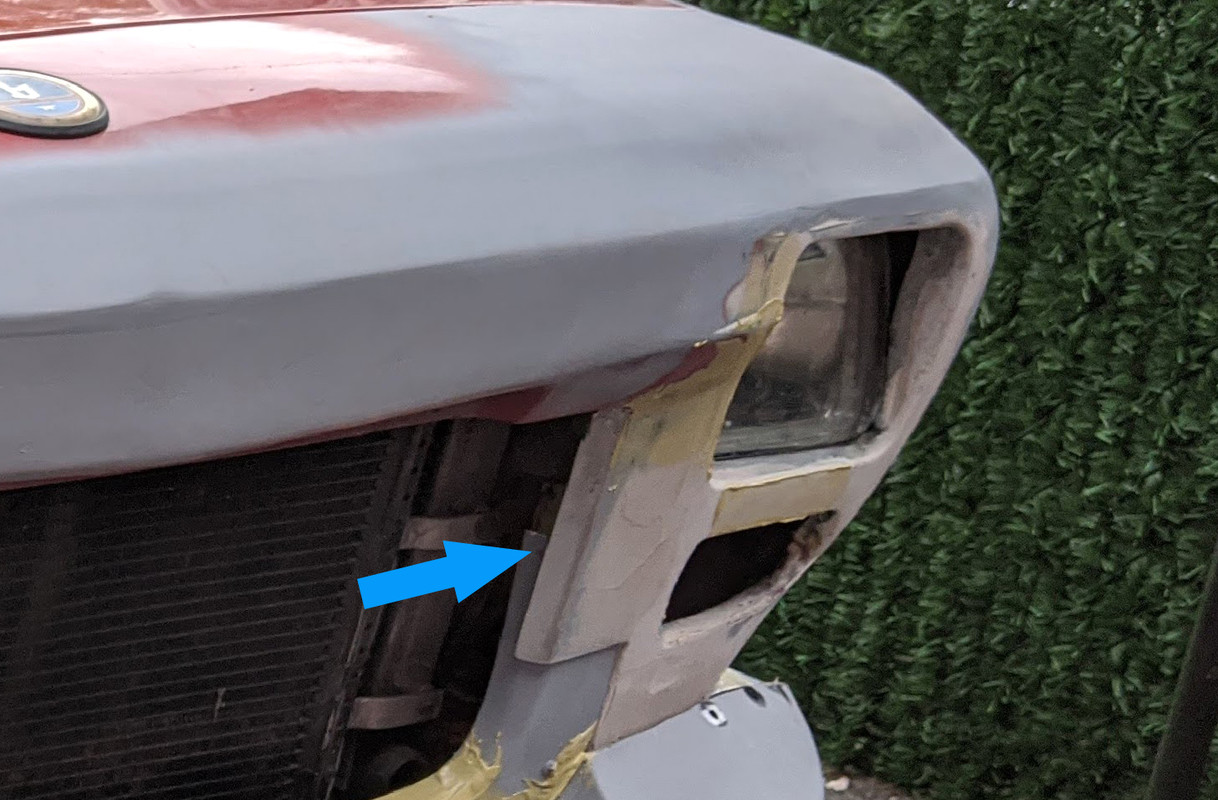
Last edited: