AKimball92
True Classic
I attempted to do a cruise last weekend but as soon as I got onto the interstate and up to speed the car began to shake. Badly Shake!!!
I have done suspension work on the car, front and rear. I did not align it prior. It tracked straight so I spent my time elsewhere. After this I went to do a string alignment and noticed front right tie rod jam nut was loose and too much toe inward.
String alignment to about .75" outboard of the front edge of the rear wheel and torqued down helped a bit. Very slight pull to the right so slight adjustments needed still, maybe a quarter/half turn after a very straight entrance to the garage.
Hit the interstate and the shake isn't as bad and now I feel the shake come from the rear as well.
Can someone help in identifying "proper" string alignment for the rear? Pics below show two different values. Severely sorry for the upsidedown pics. I ensured the phone was right-side up for being sideways. Its correct in the files and media viewer on the computer.
(this happened last time)
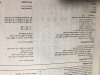
If the alignment doesn't fix it I will take the wheels for another balance. Two were done by someone I trust, the man who does the wheels and alignments for Ford Performance. The shop hand that did the first two didn't know the wheels were directional with the standard Federal V tread design...
I have done suspension work on the car, front and rear. I did not align it prior. It tracked straight so I spent my time elsewhere. After this I went to do a string alignment and noticed front right tie rod jam nut was loose and too much toe inward.

Hit the interstate and the shake isn't as bad and now I feel the shake come from the rear as well.
Can someone help in identifying "proper" string alignment for the rear? Pics below show two different values. Severely sorry for the upsidedown pics. I ensured the phone was right-side up for being sideways. Its correct in the files and media viewer on the computer.


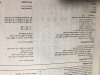
If the alignment doesn't fix it I will take the wheels for another balance. Two were done by someone I trust, the man who does the wheels and alignments for Ford Performance. The shop hand that did the first two didn't know the wheels were directional with the standard Federal V tread design...