So to continue with my version using the escort heater core (thanks to Capt. Obvious on ClassicZ) I ordered the heater valve mentioned by another -4 Seasons 74627 - but it didn't arrive until late this evening, so I dismantled the original & had a go at fixing it following the other thread on ClassicZ
Think it's pretty clear why the heat never shut off
I forgot to take pics of the re-assembly, I used a Viton o-ring in place of the square cut outer seal, I left the inner one alone. Left it set on an angle filled with fluid to check for leaks.
I flipped the I/O for the heater hoses - the bulkhead upper is now the return & the outer/lower is the feed. I did it this way so that the feed is not too short, and the return is a straighter run. and so the inside feed is a plain elbow 90º. Determining hose lengths here. An -10 fittings. SS pipe length is 20.5".
dogleg for the other end, test fit alignment of pipe & hoses
Hoses cut & clamped (head fitting was removed, de-rusted, sealed & reinstalled, slight offset change -more vertical
Far end adjusted & clamped
With that end out of the way, I returned to the heater valve & core (91-02 Ford Escort). Eyeballed holes for core pipes, based on the core being centered
Core sizing comparison pics (copper version, slighlty smaller core than the aluminum). Added closed cell foam on the sides to make it snug, and to the front to keep it pushed all the way in & cover up the old pipe holes.
Was playing with hose routing - this way was to allow the 74627 straight pipe valve to sit above the feed pipe
along these lines
I'll revert to this layout if I need to switch to the 74627 valve
When it became clear that the 74627 wasn't coming , I switched gears & worked on fitting the original repaired valve -
Heater valve fitted using the upper existing mount screw, new hole drilled in plate. Cut a notch in the valve mount bracket to clear the lower screw. Checked that flap can open.
Feed hose clamped. Cable attached & function tested.
Test fitting (formed, Volvo) hoses to & from heater valve
Added oetiker clamps after this. Since I wasn't able to flare the end of the core tubing, I prefer them as the clamping is typically more uniform than a worm clamp of any type.
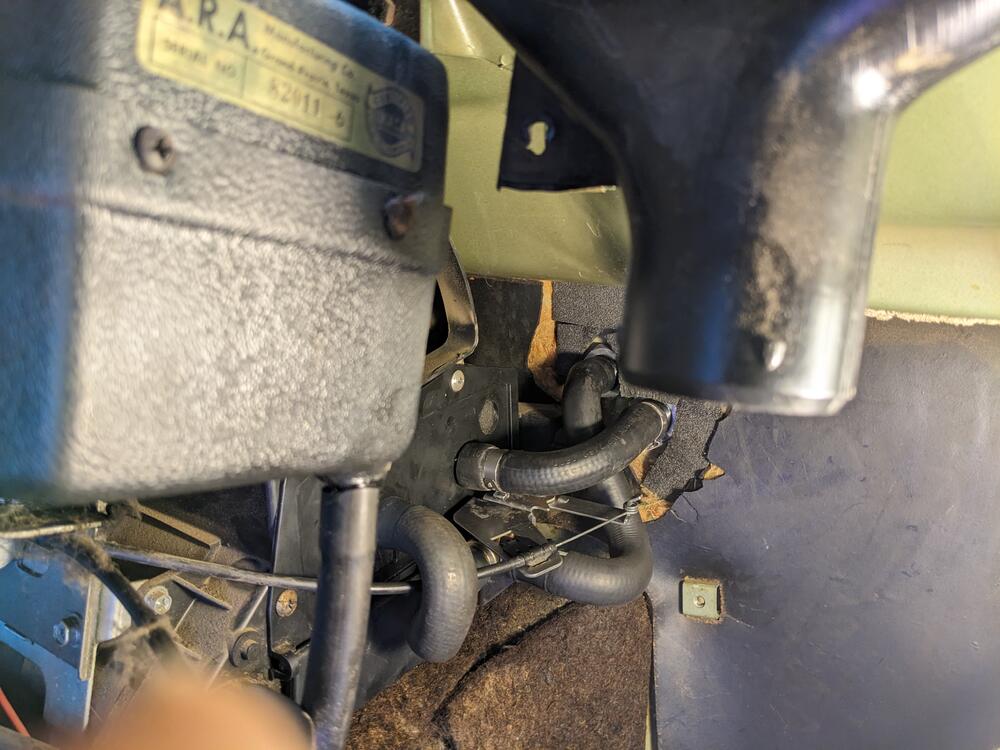