lookforjoe
True Classic
Had a little time to work on the dash today, so I put the frame in the car to figure out the right side support brace
Left side brace sits right up against the box
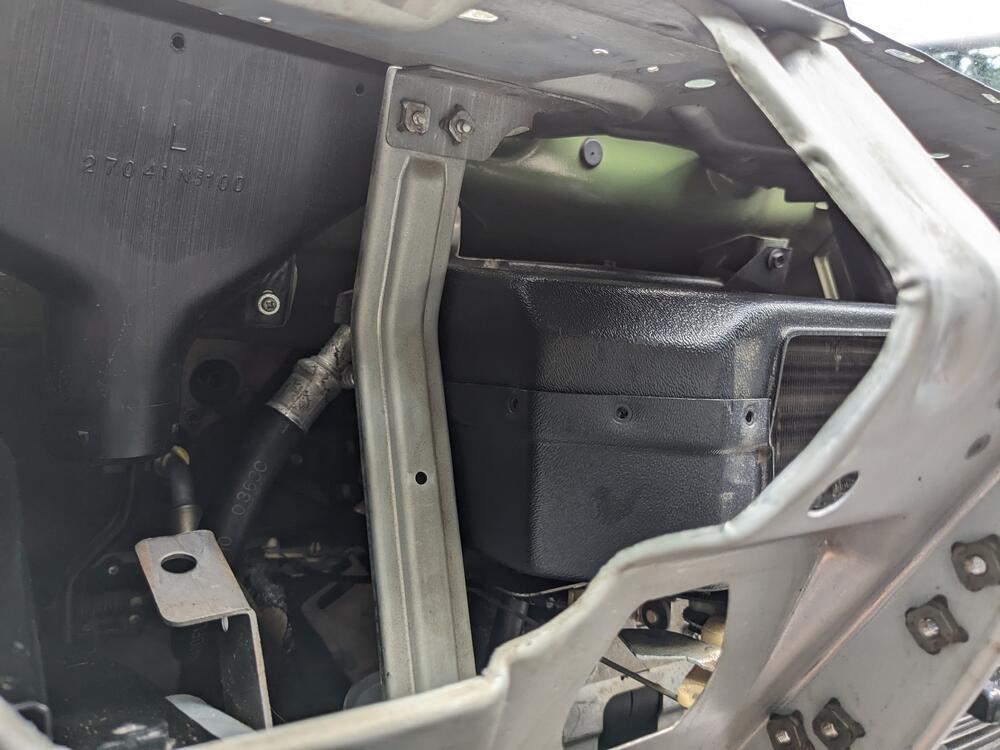
Right side - definitely was removed due to Evaporator
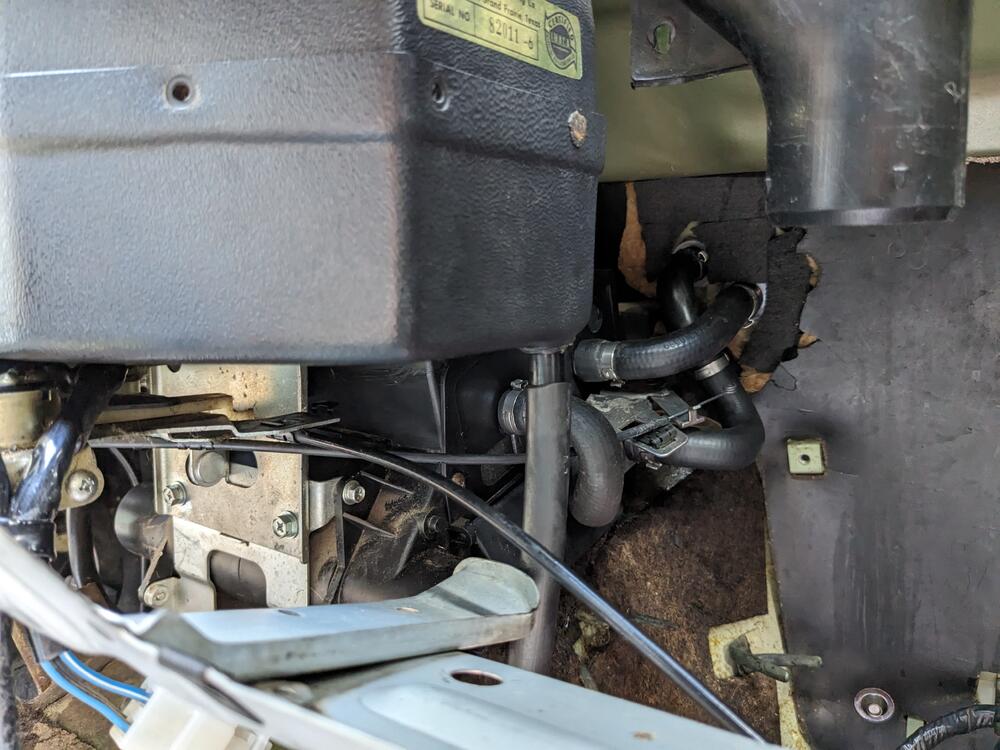
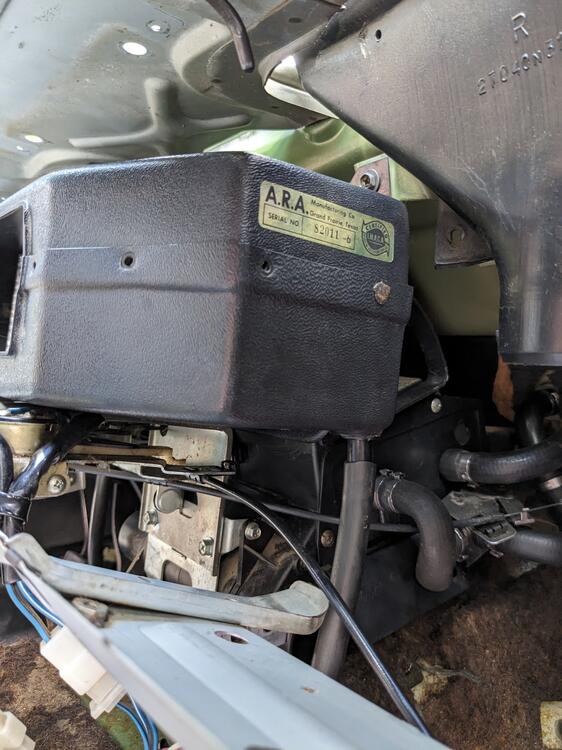
set the glovebox in place, to check clearance outside the evaporator box - none
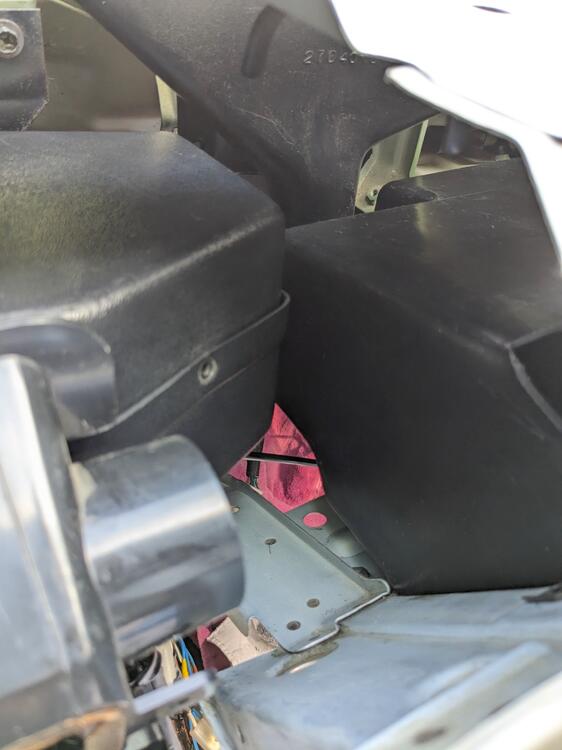
Used a aluminum ruler to make a brace
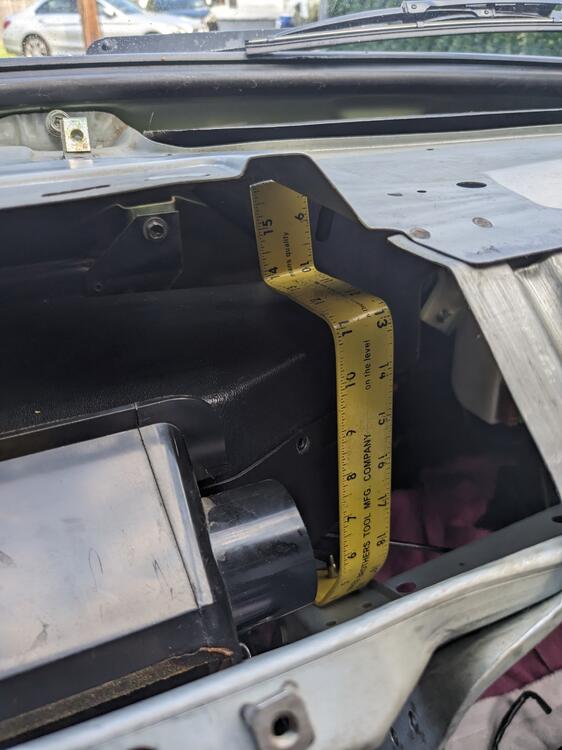
I'll add an angle bracket back to the dash frame, to attach the brace to
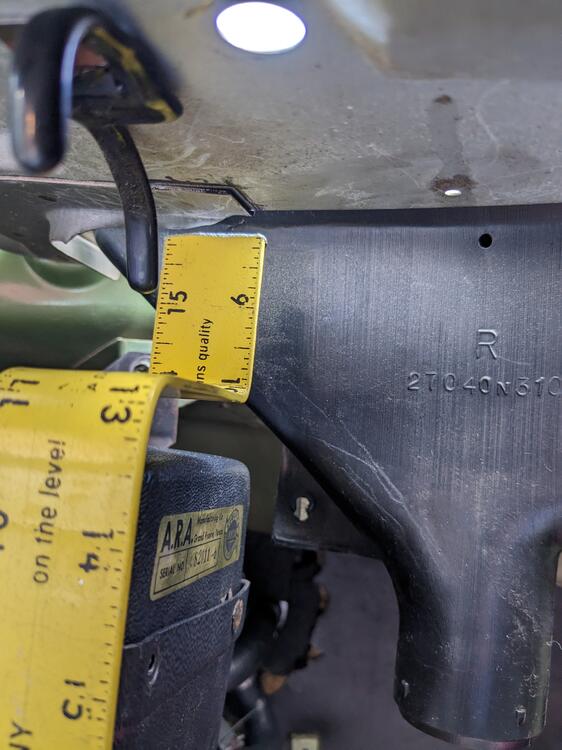
frame back out to finish up the angle bracket for the brace & add spot welds to the existing structure
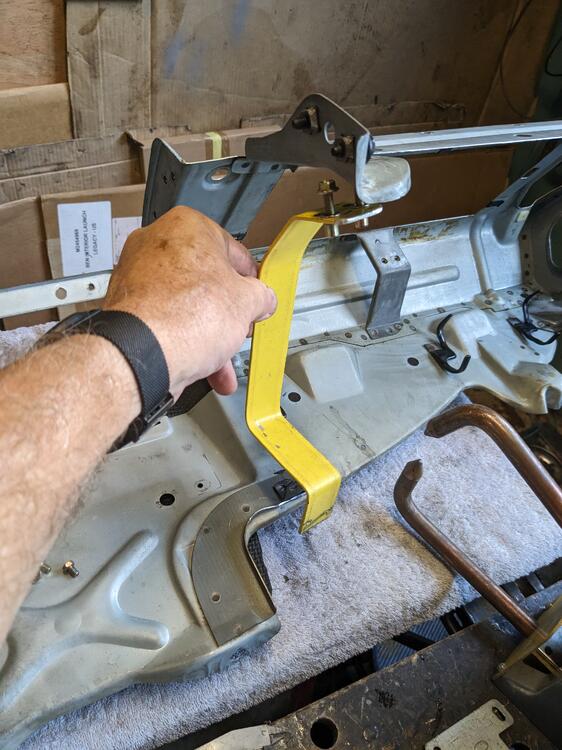
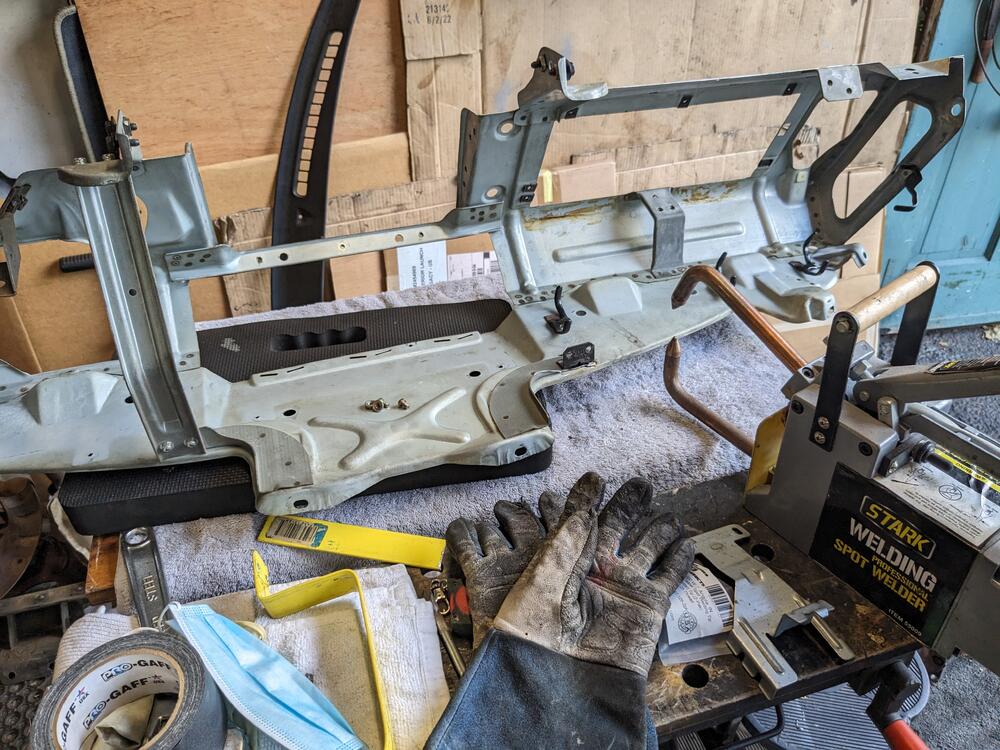
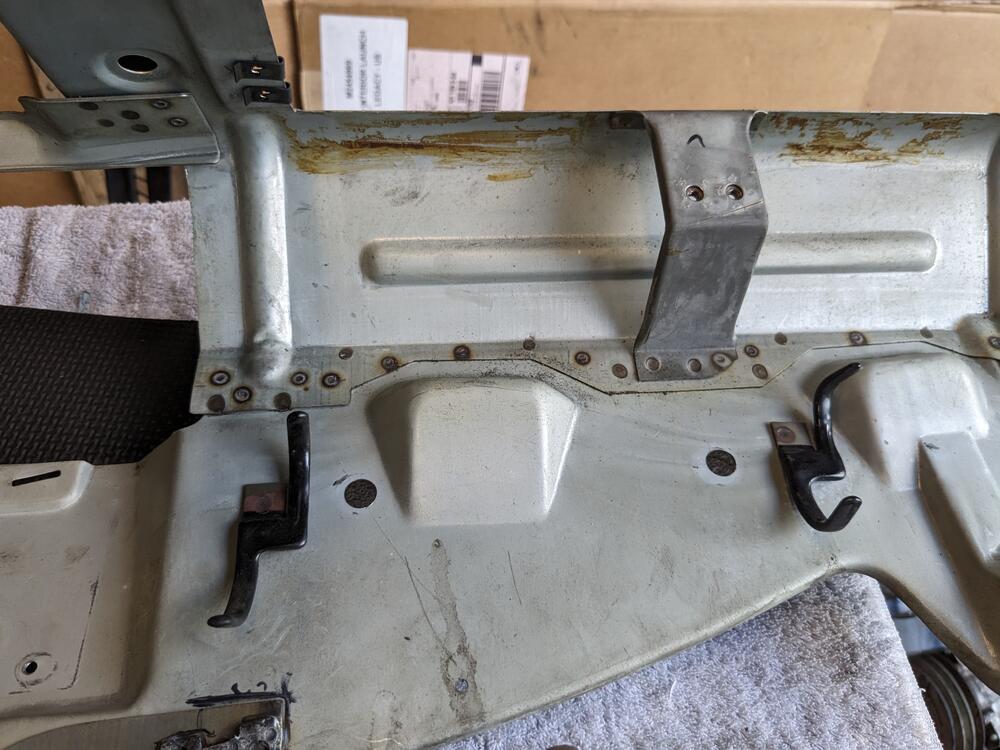
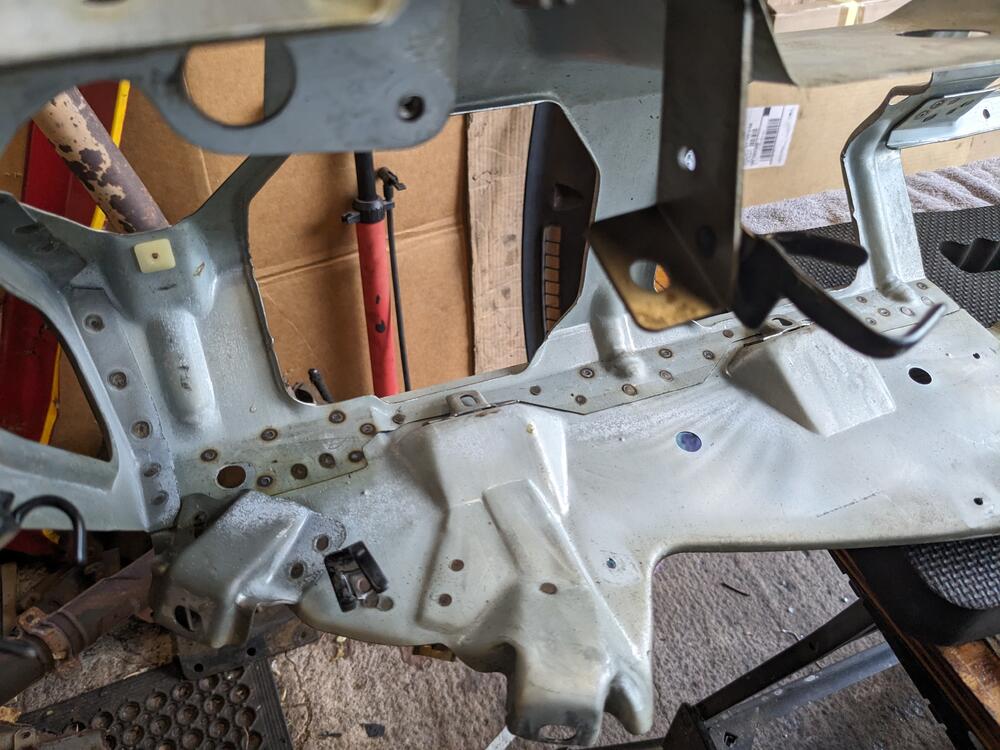
Going to replace the fusebox with an MTA 15 ATC fusebox, and a (4) relay panel
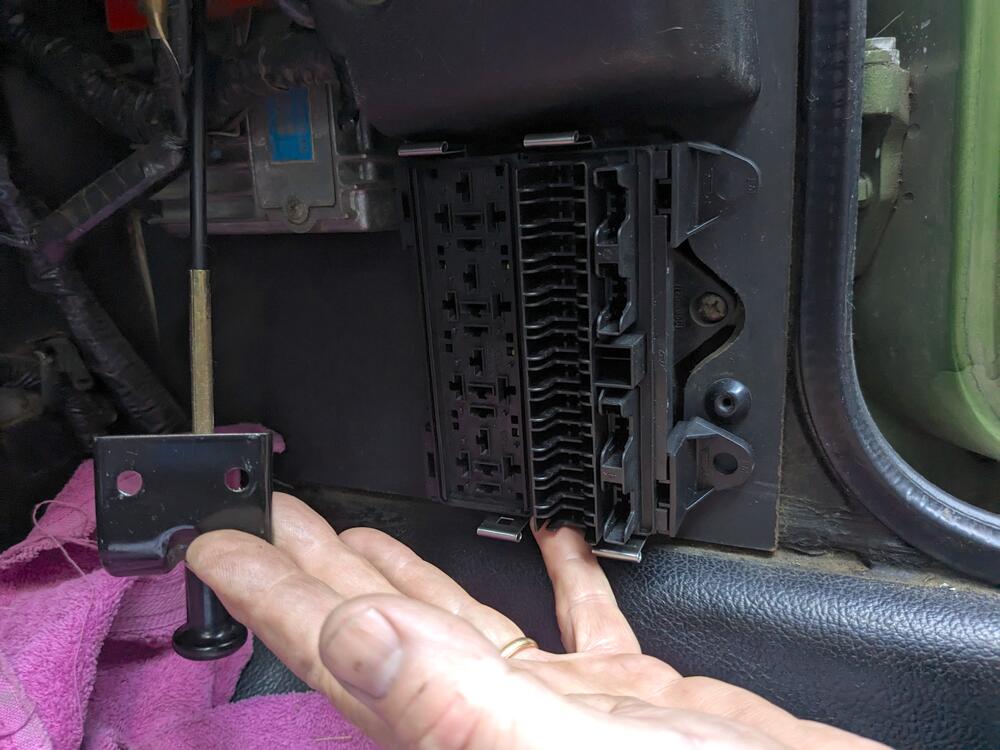
l
Left side brace sits right up against the box
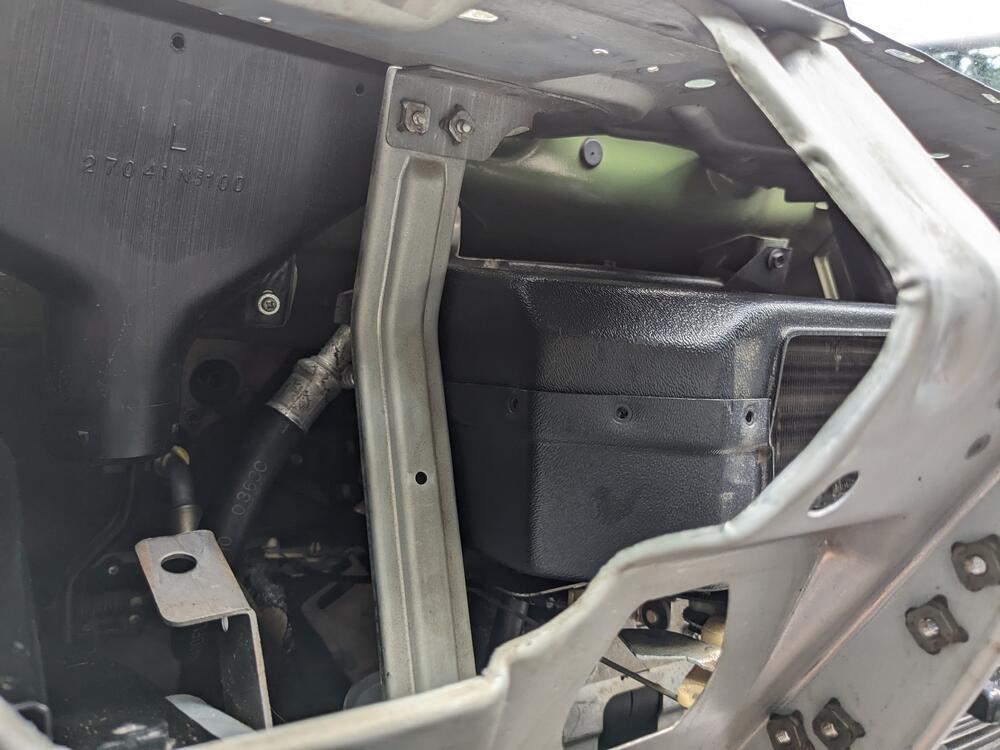
Right side - definitely was removed due to Evaporator
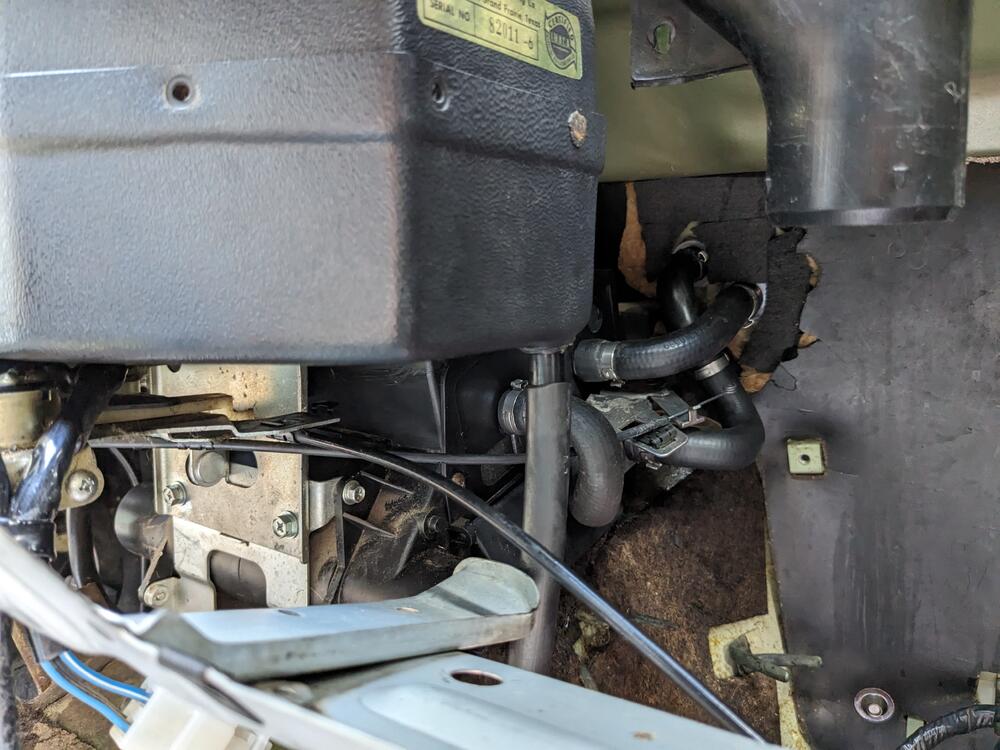
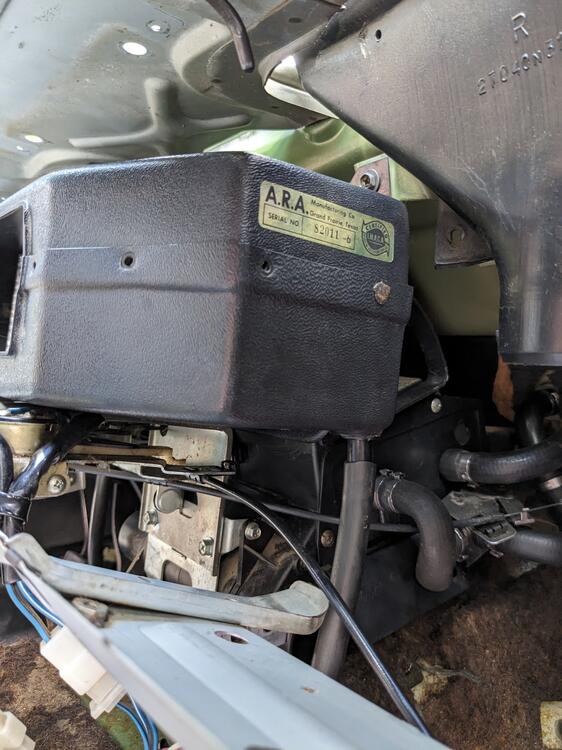
set the glovebox in place, to check clearance outside the evaporator box - none
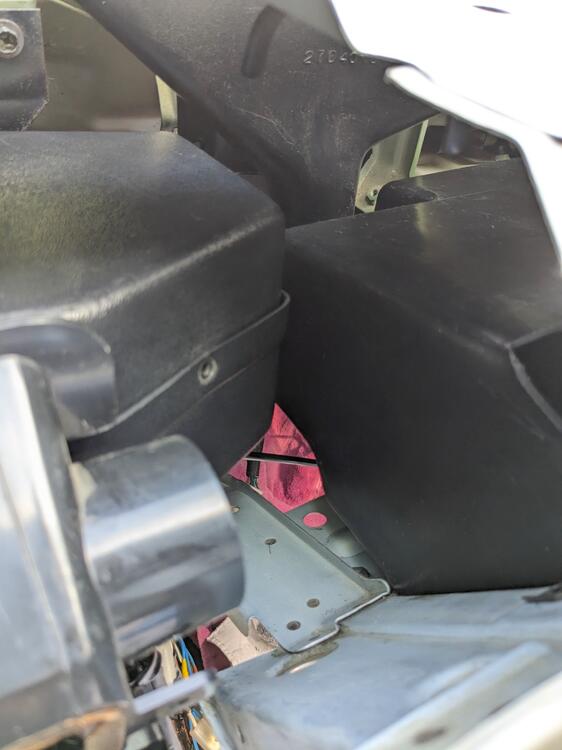
Used a aluminum ruler to make a brace
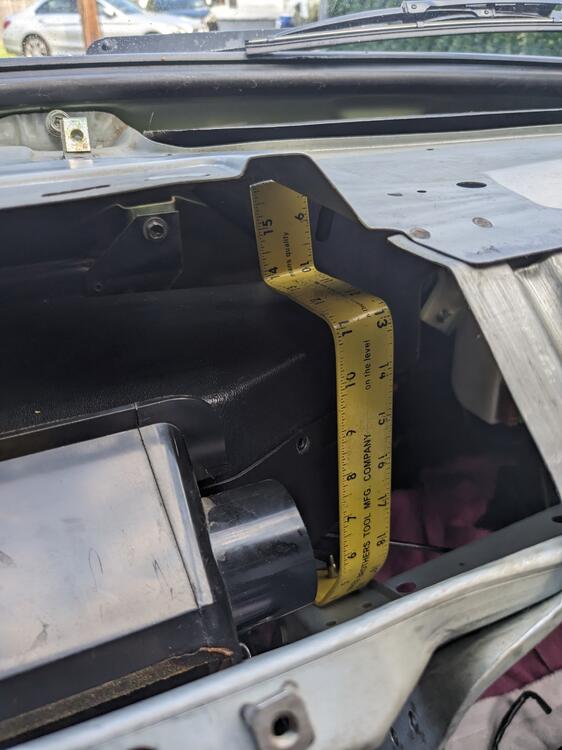
I'll add an angle bracket back to the dash frame, to attach the brace to
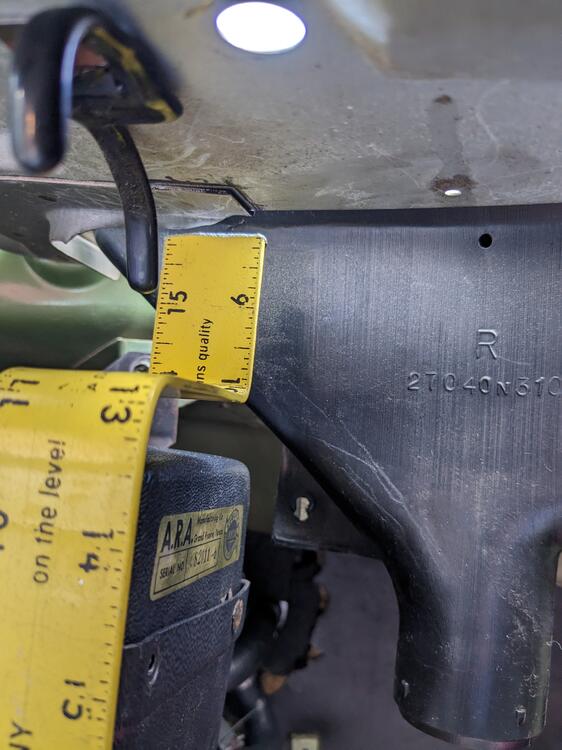
frame back out to finish up the angle bracket for the brace & add spot welds to the existing structure
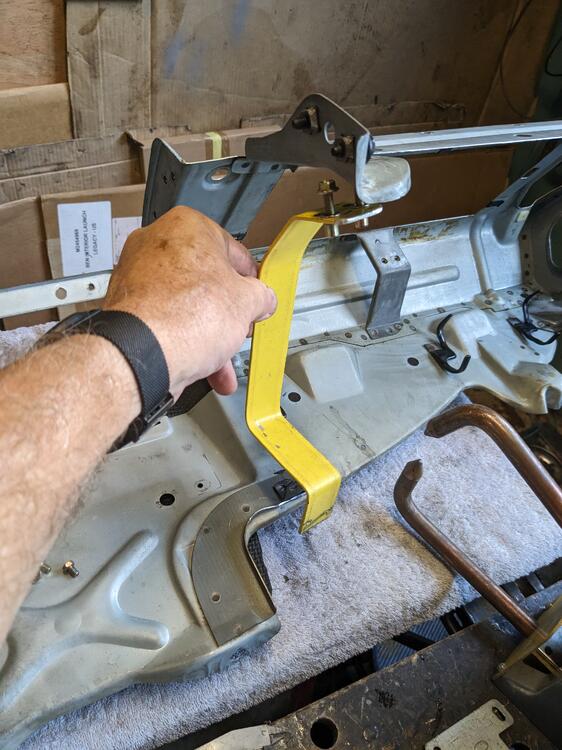
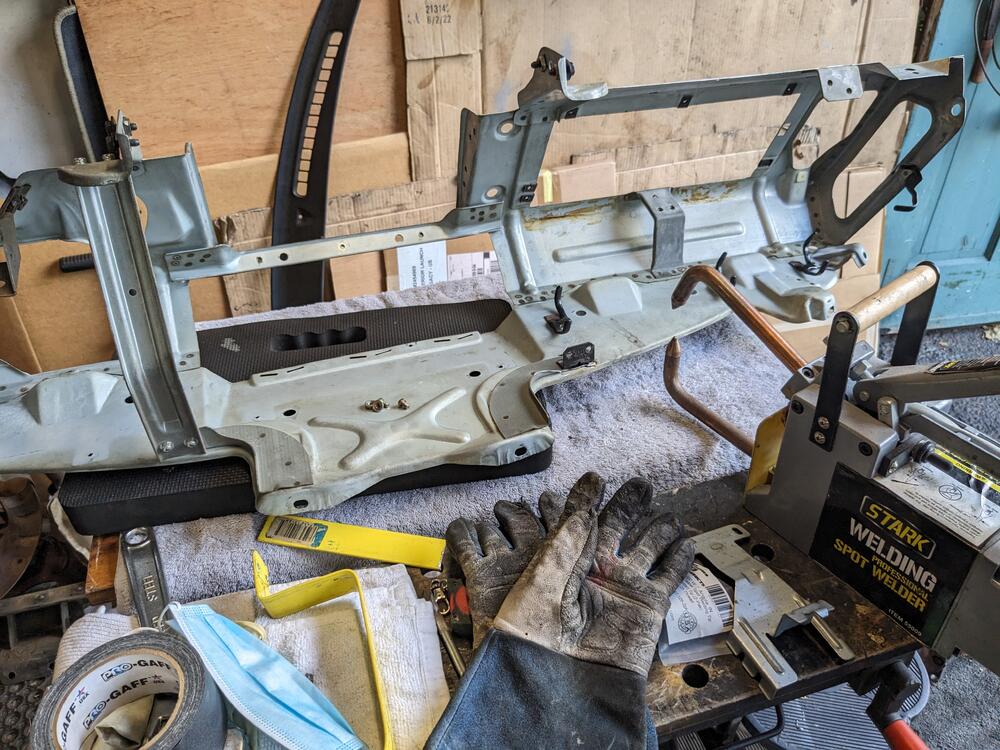
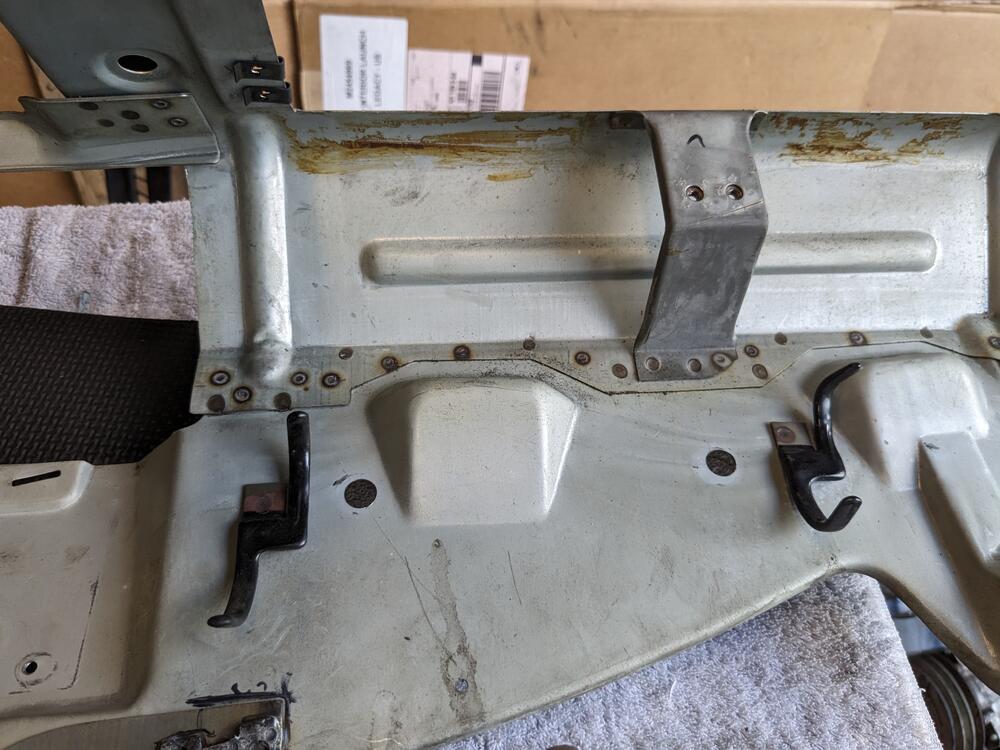
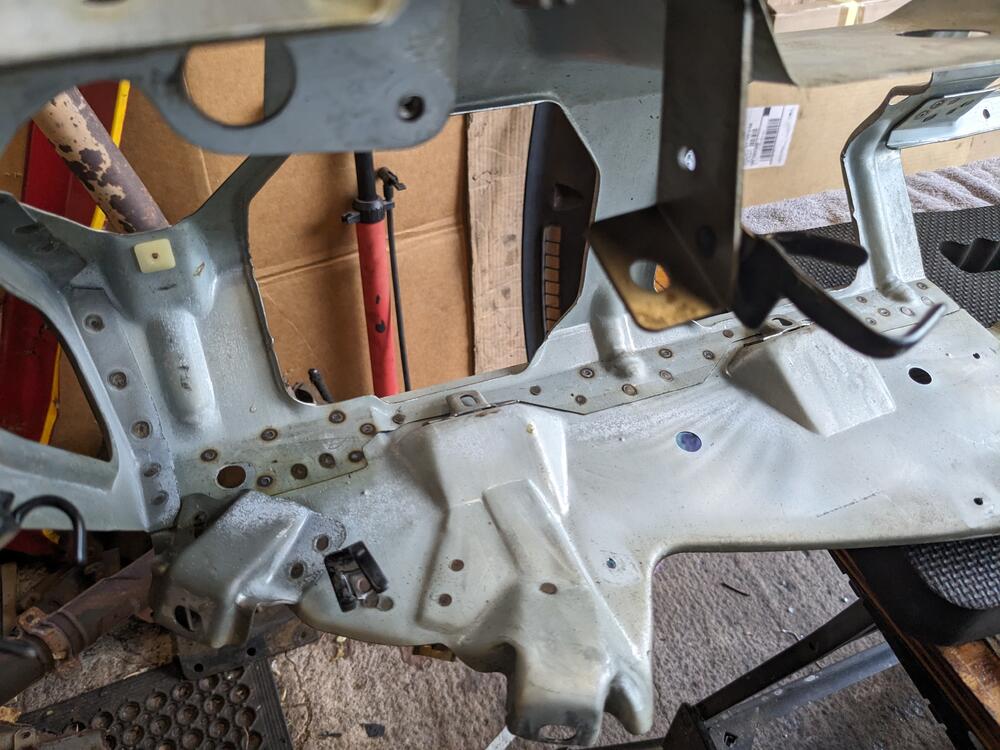
Going to replace the fusebox with an MTA 15 ATC fusebox, and a (4) relay panel
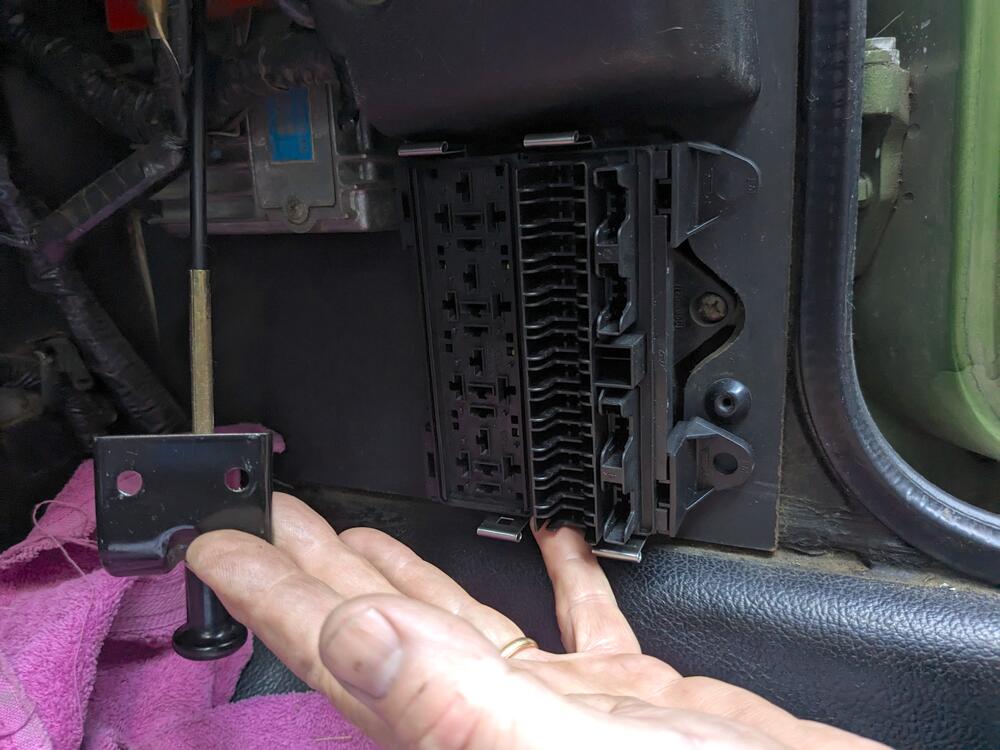
l