lookforjoe
True Classic
Took the rear struts & hubs apart after doing the Fuel pump setup. Removed the drum brake back plates that are no longer needed.
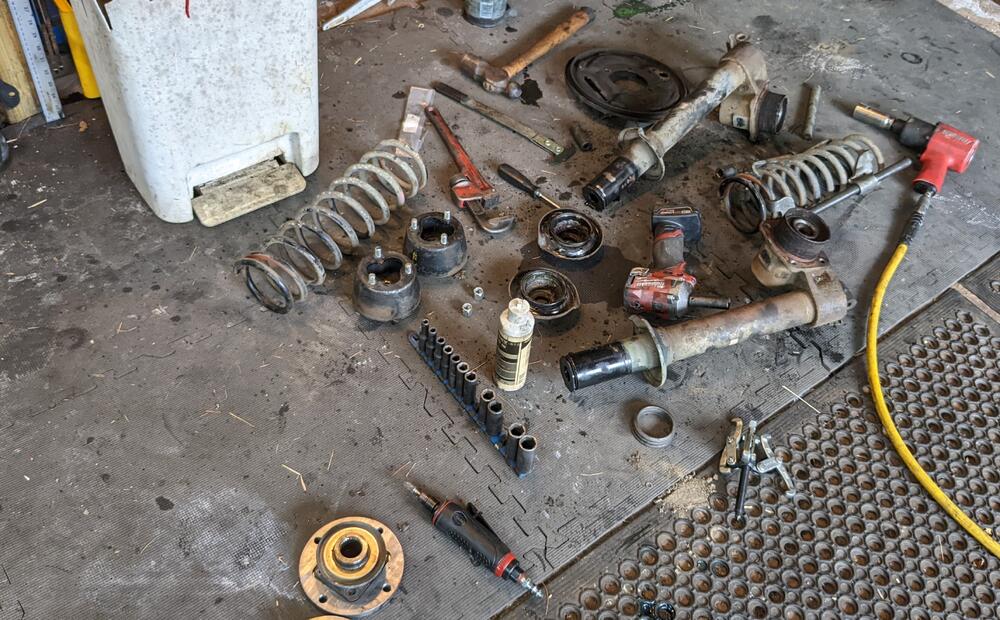
cut down the nub of the spindle, to make sure the Z31 CV cap doesn't hit
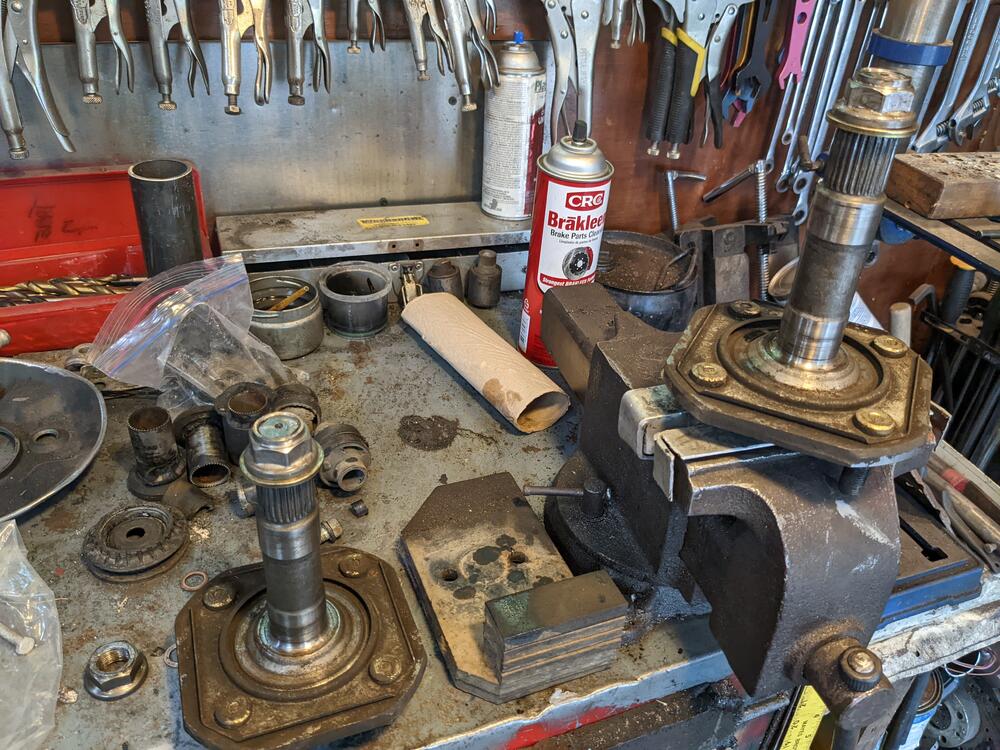
removed the (too short) wheel studs & cleaned the outer flanges
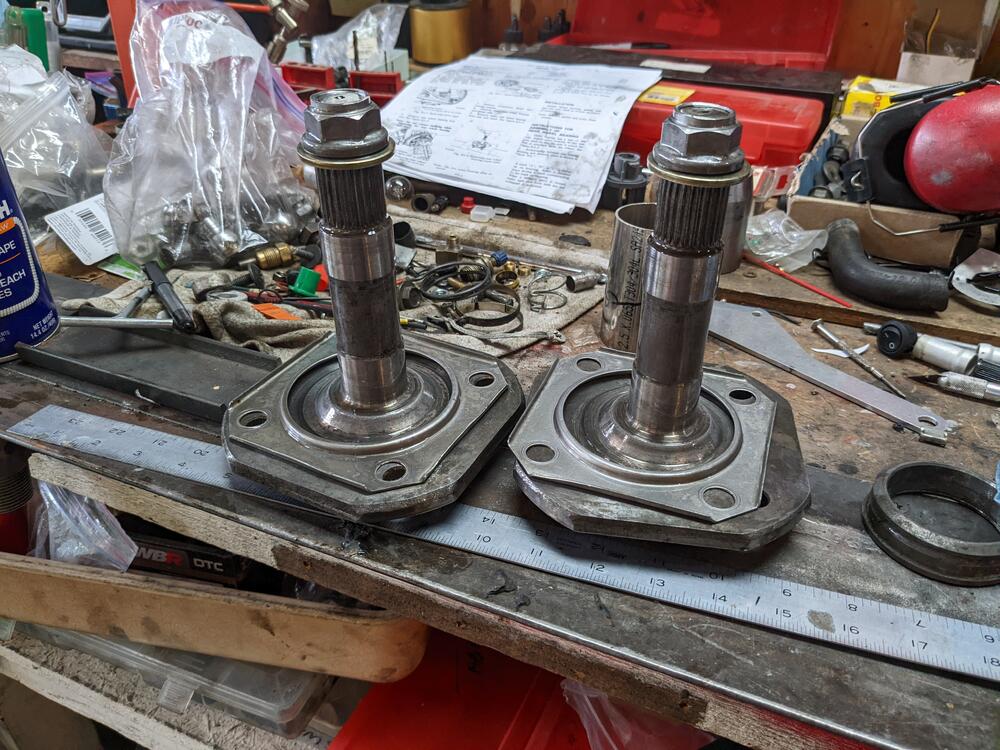
Still not happy with not having a hub seat for the wheels
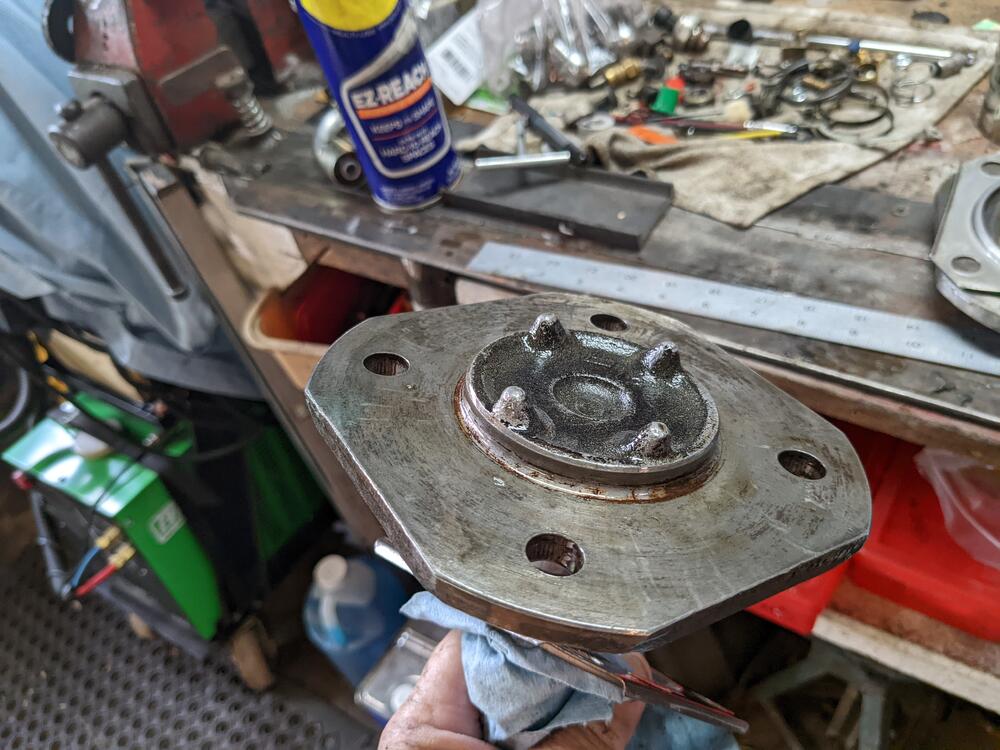
I may weld on a sleeve (cut from a Volvo), that will allow me to use a hub centric ring (65.1 - 73.1) to set the Konig wheels. Have to have the nubs turned down in that case, to get a good seat for welding
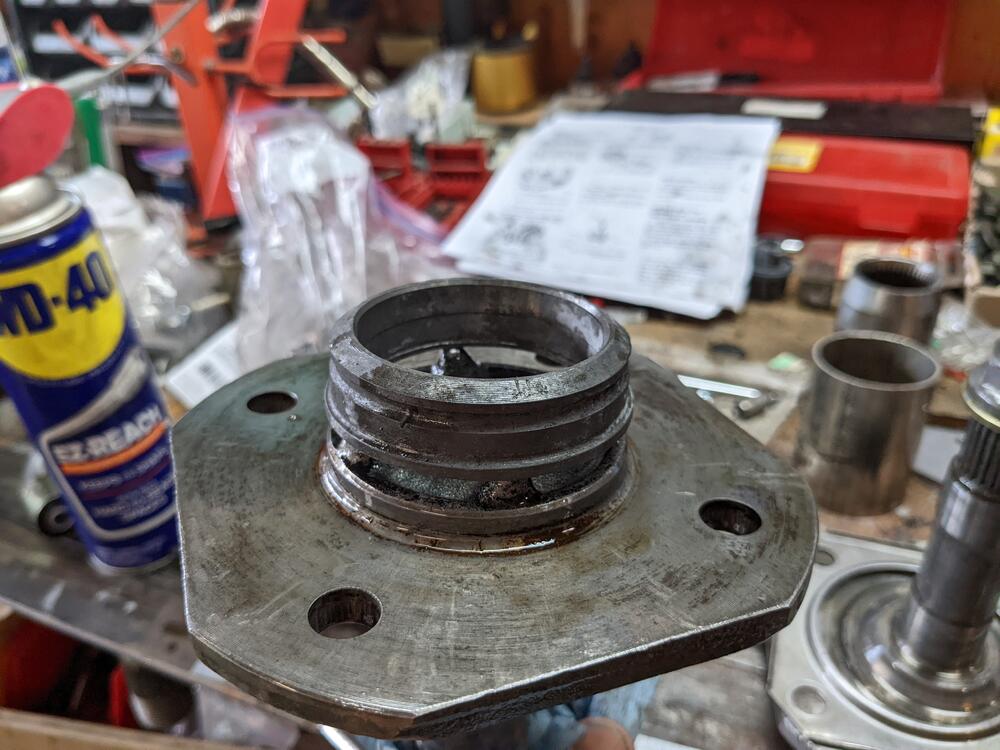
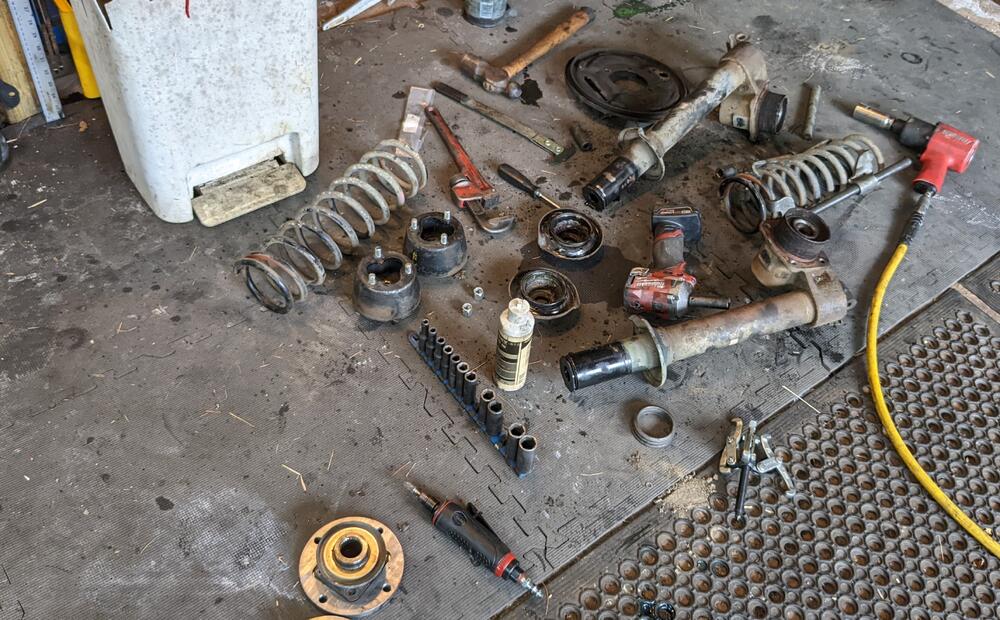
cut down the nub of the spindle, to make sure the Z31 CV cap doesn't hit
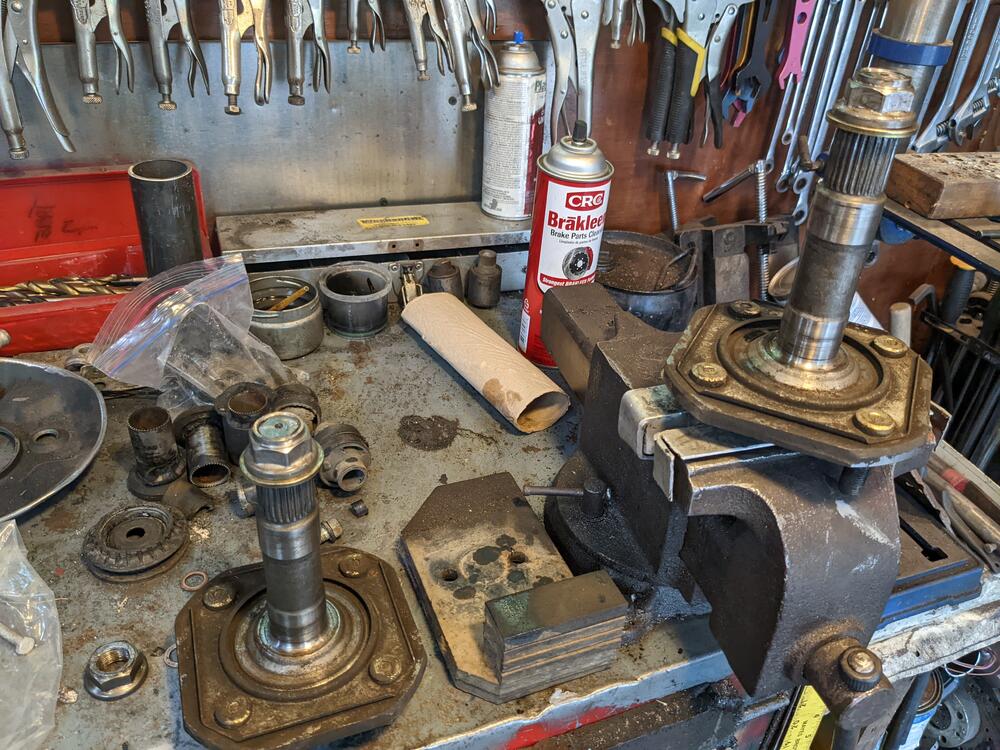
removed the (too short) wheel studs & cleaned the outer flanges
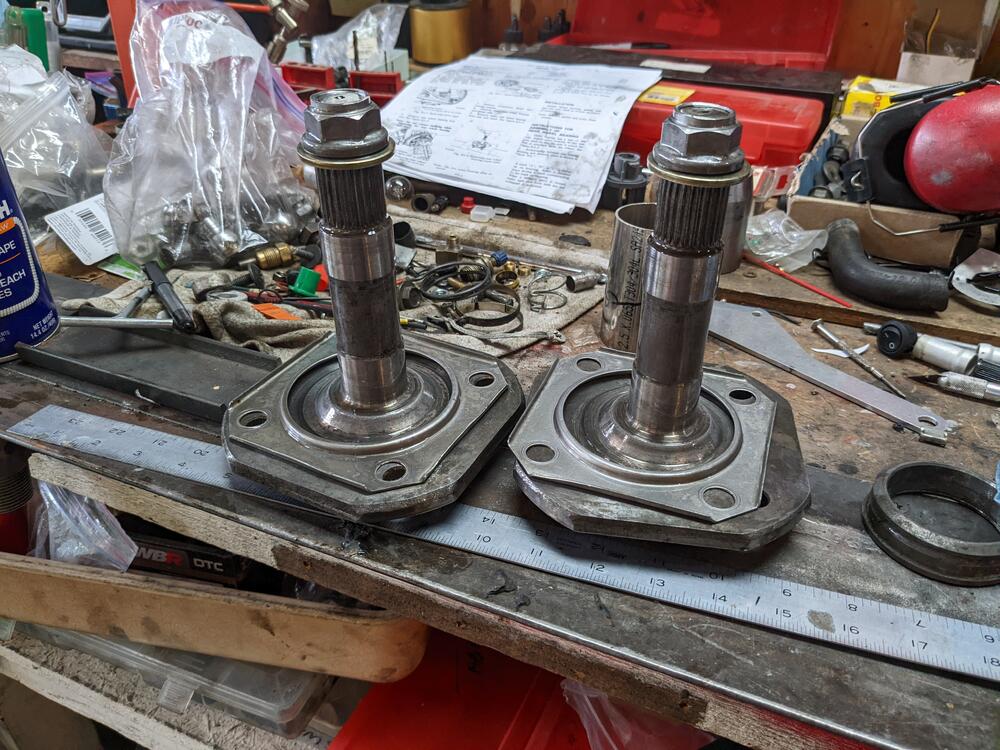
Still not happy with not having a hub seat for the wheels
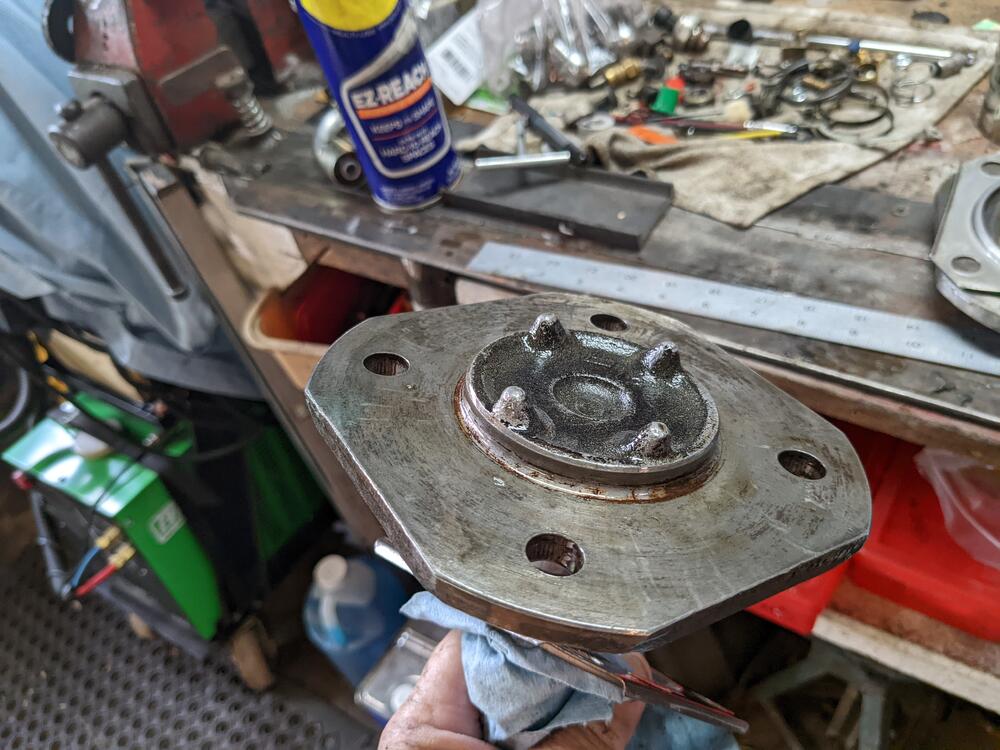
I may weld on a sleeve (cut from a Volvo), that will allow me to use a hub centric ring (65.1 - 73.1) to set the Konig wheels. Have to have the nubs turned down in that case, to get a good seat for welding
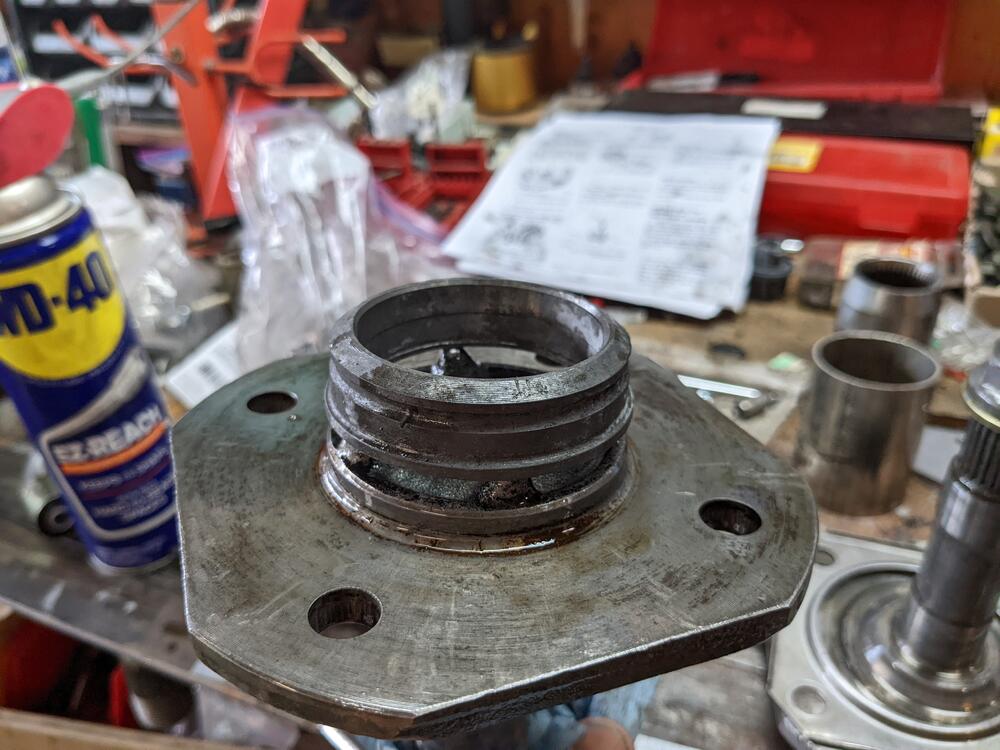