lookforjoe
True Classic
New lamp gaskets finally arrived, so I reinstalled my tail light panels back onto the tail lamps. I will need to source new ones DTR, they are so brittle, they keep cracking when I handle them. Also had to use 3M VHB tape to glue the panels the lamps, as most of the screw mount posts are so brittle they snapped & crumbled when I tried to reinstall them.

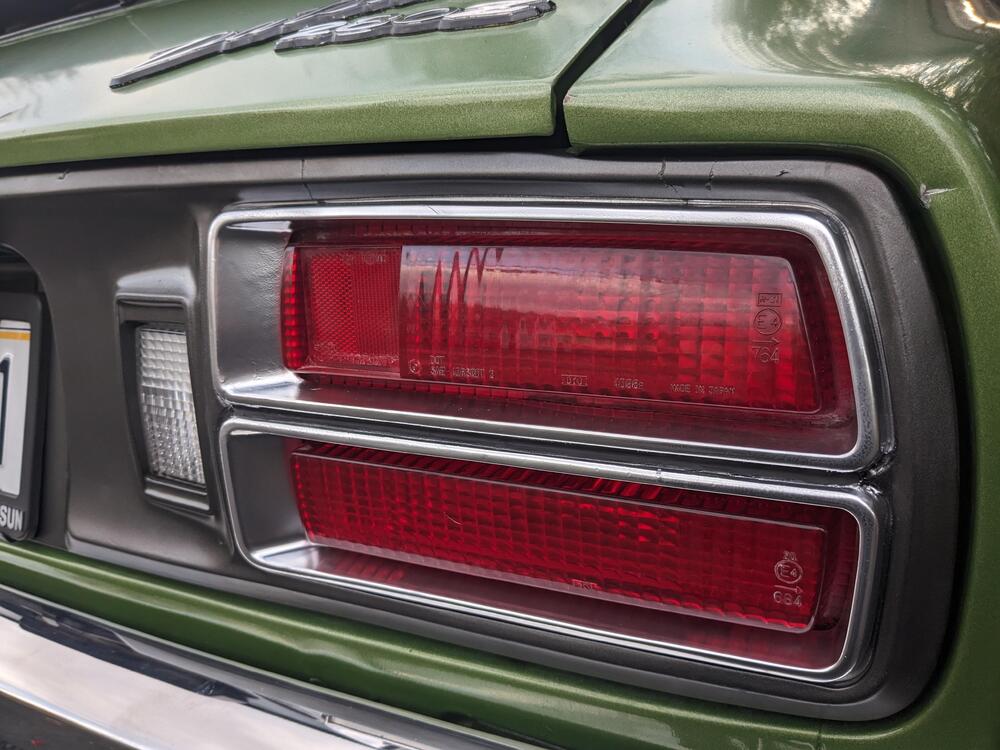
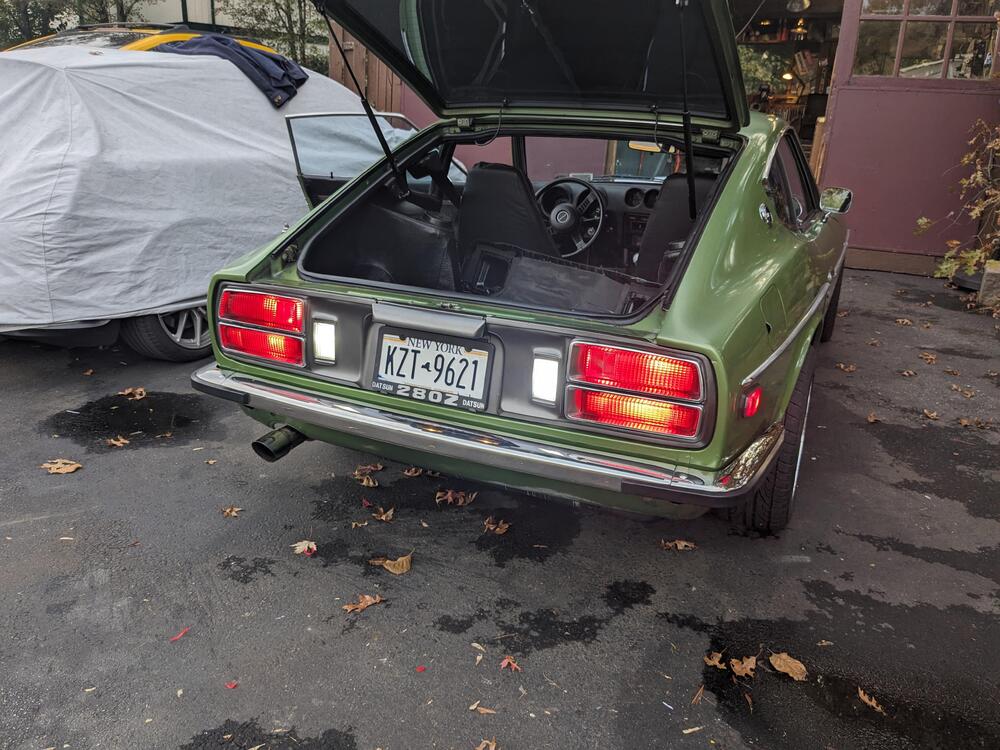
with those installed, I was able to put the rear panel back in. I added closed cell foam to give some more density
all back together - hopefully its quieter with the tail panel back in

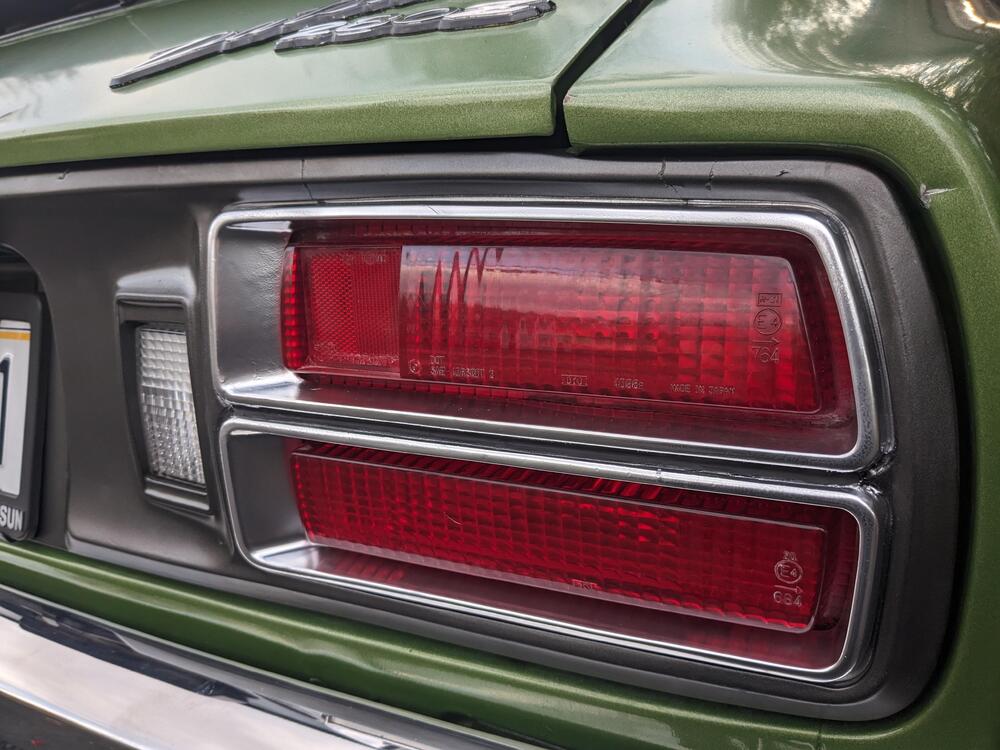
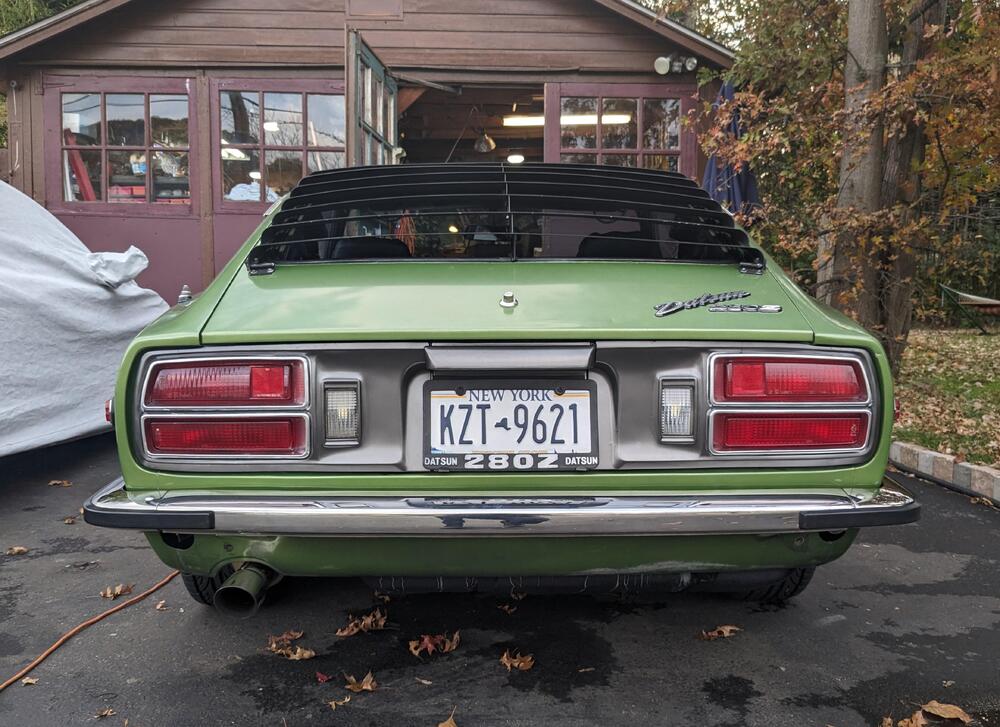
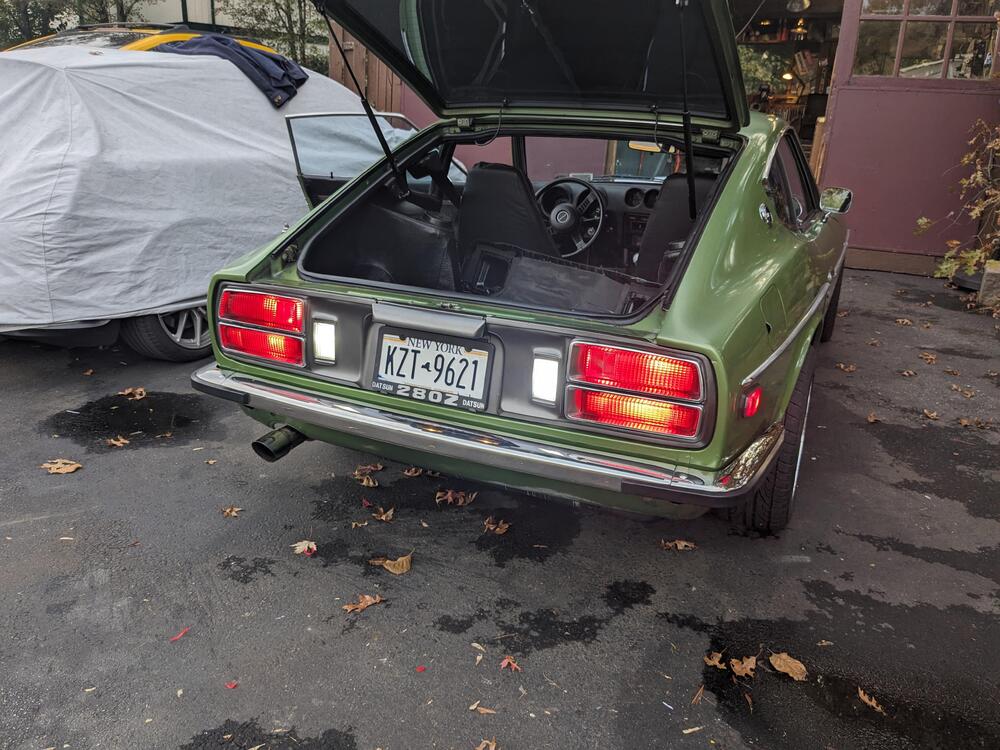
with those installed, I was able to put the rear panel back in. I added closed cell foam to give some more density
all back together - hopefully its quieter with the tail panel back in
Last edited: