rx1900
1981 X1/9
Hi folks. As part of my restoration, I decided to re-fresh the suspension of my X1/9. Like many of yours....the car had been sitting for quite a few years. The suspension parts were looking somewhat rusty,and the bushings and boots were old, tired, hardened, and cracked in places. I also built some fancy coilovers and got some zoomy wheels and tires.
I figured it was best to start with a solid foundation. All the ball joints seemed okay with no play. But after 40 years...I figured it was time for a good cleaning, painting, servicing, and re-greasing. I'm happy I did.
I eventually rounded up all the bits I needed. That was quite the ordeal. And offered them up in complete packages here:
And when they sold out another offering here:
So lets get started.....
The front suspension is much easier to do than the rear. So lets start there. Luckily..the X1/9 has a very simple front suspension. In fact...way simpler than most cars.
Tools needed: Not much special really.
you will find it easier with an impact wrench in places. Air or electric. I used one of those electric ones. They are just so handy to have around. Great for changing wheels. If you dont have one...they are cheap..like $50 at Harbor Freight.
You will have to separate the ball joints and tie rod ends. There are several methods. Some folks manage with pair of hammers. I found it easiest with a "ball joint seperater" tool. Like one of the ones below.
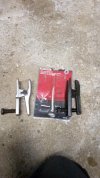
I found the black one worked better. It is an Autocraft AC3430. Only $20.
Both were from Princess Auto up here ( the Canadian equivalent of Harbor Freight ).
I suppose this type might work well in places:
Do NOT use a "'pickle fork" type tool. As that will usually damage the ball joints innards !!
Other than that...you will only need a few sockets and end wrenches.....and a decent bench vise.
Okay...lets start.
Jack up the front end of the car and support securely on jack stands.
Remove the wheels.
It is probably best to start with the front outer tie rod ends. Yank on them and see if you feel any play. Of course...if you detect any play...you will have to replace them. They are available pretty cheap. But...if no play....I would prefer to just re-fresh the existing ones. Two reasons...first...it has long been felt that the original tie rod ends were a much better quality than the available replacements. And second...just re-freshing them can easily be done on the car...without removing them...so no need for an alignment later.
Undo the nut ( using a 17mm wrench or socket ) until it the bottom of it is below the threaded part. Do this so the tool will then press on the nut. If you remove the nut entirely at this point the tool would then press against the ends of the thread and possibly damage the end threads. Then insert the tool and tighten it until the joint pops.
Then undo the nut and rest the tie rod end as shown on the upright. Then with a screwdriver tap the boot off.
Flip it back over and take a look. Ouch....mine was all dry inside...no grease in sight !!! Just some hardened bits. Left like that....surely the joint would not have lasted long at all !!!
At this point.....check again the joint for any play. Easy to tell now.
Clean it up as best you can with rags and a small wire brush:
Work in some grease as best you can.
Clean off the landing spot of the new tie rod end boot. And apply some grease to the small inner end of the boot. Place new boot in position.
As this boot type is pressed on to the joint....you must then drive it home. Use a 30mm deep socket and with a hammer, tap it on until it is firmly seated
Flip it over and install into the upright with the new nyloc from the kit. Note !!! it takes a m10 x 1.25 short type nyloc !!! There is also in the kit a m10 x 1.25 TALL type nyloc which is for the lower control arm pivot bolt. Make sure you use the correct short type here on the tie rod end...and leave the TALL type for later !!!
Torque the nut to 25 ft-lbs...and you are done !!! That was easy.....
all done:
Now the above is assuming that your X has the press-on type boots as shown. But most replacement tie rod ends seemed to have come with a boot that was instead held on with two funky wire clips. I will explain how to deal with them in the next episode.
In the next installment we will move onto the lower control arms and radius rod. Stay tuned.....
I figured it was best to start with a solid foundation. All the ball joints seemed okay with no play. But after 40 years...I figured it was time for a good cleaning, painting, servicing, and re-greasing. I'm happy I did.
I eventually rounded up all the bits I needed. That was quite the ordeal. And offered them up in complete packages here:
Fiat X1/9 suspension re-fresh kits
Update April 23/22.....available again here: https://xwebforums.com/forum/index.php?threads/fiat-x1-9-and-lancia-scorpion-suspension-re-fresh-kits-available-again.42286/ Hi Folks. Well I am proud to present my latest project. This time it is complete suspension re-fresh kits. Typically one...
xwebforums.com
And when they sold out another offering here:
Fiat X1/9 and Lancia Scorpion suspension re-fresh kits available again !
Note this may be considered a commercial post. Hi Folks. Good news. Yup...as the title suggests....my famous suspension re-fresh kits are available again. What with world-wide supply chain issues...it has been a struggle to accumulate all the bits needed for these kits. Some of the...
xwebforums.com
So lets get started.....
The front suspension is much easier to do than the rear. So lets start there. Luckily..the X1/9 has a very simple front suspension. In fact...way simpler than most cars.
Tools needed: Not much special really.
you will find it easier with an impact wrench in places. Air or electric. I used one of those electric ones. They are just so handy to have around. Great for changing wheels. If you dont have one...they are cheap..like $50 at Harbor Freight.
You will have to separate the ball joints and tie rod ends. There are several methods. Some folks manage with pair of hammers. I found it easiest with a "ball joint seperater" tool. Like one of the ones below.
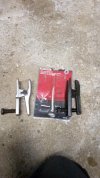
I found the black one worked better. It is an Autocraft AC3430. Only $20.
Both were from Princess Auto up here ( the Canadian equivalent of Harbor Freight ).
I suppose this type might work well in places:
Do NOT use a "'pickle fork" type tool. As that will usually damage the ball joints innards !!
Other than that...you will only need a few sockets and end wrenches.....and a decent bench vise.
Okay...lets start.
Jack up the front end of the car and support securely on jack stands.
Remove the wheels.
It is probably best to start with the front outer tie rod ends. Yank on them and see if you feel any play. Of course...if you detect any play...you will have to replace them. They are available pretty cheap. But...if no play....I would prefer to just re-fresh the existing ones. Two reasons...first...it has long been felt that the original tie rod ends were a much better quality than the available replacements. And second...just re-freshing them can easily be done on the car...without removing them...so no need for an alignment later.
Undo the nut ( using a 17mm wrench or socket ) until it the bottom of it is below the threaded part. Do this so the tool will then press on the nut. If you remove the nut entirely at this point the tool would then press against the ends of the thread and possibly damage the end threads. Then insert the tool and tighten it until the joint pops.
Then undo the nut and rest the tie rod end as shown on the upright. Then with a screwdriver tap the boot off.
Flip it back over and take a look. Ouch....mine was all dry inside...no grease in sight !!! Just some hardened bits. Left like that....surely the joint would not have lasted long at all !!!
At this point.....check again the joint for any play. Easy to tell now.
Clean it up as best you can with rags and a small wire brush:
Work in some grease as best you can.
Clean off the landing spot of the new tie rod end boot. And apply some grease to the small inner end of the boot. Place new boot in position.
As this boot type is pressed on to the joint....you must then drive it home. Use a 30mm deep socket and with a hammer, tap it on until it is firmly seated
Flip it over and install into the upright with the new nyloc from the kit. Note !!! it takes a m10 x 1.25 short type nyloc !!! There is also in the kit a m10 x 1.25 TALL type nyloc which is for the lower control arm pivot bolt. Make sure you use the correct short type here on the tie rod end...and leave the TALL type for later !!!
Torque the nut to 25 ft-lbs...and you are done !!! That was easy.....
all done:
Now the above is assuming that your X has the press-on type boots as shown. But most replacement tie rod ends seemed to have come with a boot that was instead held on with two funky wire clips. I will explain how to deal with them in the next episode.
In the next installment we will move onto the lower control arms and radius rod. Stay tuned.....
Attachments
Last edited: